Composition and Functions of Boiler Basic Components
Main Components (Steam Drum, Heating Surface, Header, Pipes) Furnace: Furnace, Burner, Air Preheater, Flue Gas Duct Boiler Body: Economizer, Steam Drum, Downcomer, Header, Water Wall, Superheater, Reheater, etc.
I. Steam Drum
The steam drum (also called the boiler drum) is the most critical pressure component in a natural circulation boiler. Its functions include:
1. Acting as the connecting hub for the heating, evaporation, and superheating processes, ensuring normal water circulation in the boiler.
2. Featuring internal steam-water separation and continuous blowdown devices to ensure steam quality.
3. Holding a certain water volume with heat storage capacity to mitigate the rate of steam pressure changes.
4. Equipping pressure gauges, water level indicators, emergency blowdown, safety valves, and other devices to ensure boiler safety.
The steam drum operates as follows: The mixture of steam and water from the water wall enters the top of the steam drum through pipes, flows down along the narrow annular channel formed by the inner wall of the drum and the arc-shaped baffle, uniformly transferring heat to the inner wall of the drum at an appropriate flow rate. This overcomes the difficulty of large temperature differences between the upper and lower walls of the drum during boiler start-up, allowing for faster startup. The steam-water mixture entering the drum is directed to steam-water cyclone separators, where the inertia during flow direction changes causes inertial separation, the first separation of the steam-water mixture. The separated steam still contains a significant amount of water and enters the corrugated plate separator from the top of the cyclone separator. This separator, mounted on top of the cyclone separator, allows steam with water droplets to flow through gaps between corrugated plates. By causing water to adhere to the metal surface and form a film flowing downwards, water droplets are separated again, known as the second separation. The steam after the second separation undergoes steam cleaning and gravity separation using the density difference of water, constituting the third separation. After three separations, the steam meets the quality standards and is then directed to the screen-type superheater through the saturated steam pipe at the top of the steam drum.
II. Heating Surface
The boiler and furnace are interconnected through the heat transfer process. The boundary between the boiler and furnace is the heating surface, which conducts heat from the heat-releasing medium (flame, smoke gas) to the heat-receiving medium (water, steam, or air). The heating surface absorbs heat from the heat-releasing medium and releases heat to the heat-receiving medium.
The heating surface, continuously absorbing and releasing heat, is called an inter-wall heating surface, where the heat-releasing medium and the heat-receiving medium are on opposite sides of the heating surface. If the heat-releasing medium and heat-receiving medium alternately and periodically contact the heating surface, releasing or absorbing heat from the heating surface during contact, it is called a regenerative heating surface. The heating surface that mainly absorbs heat from the heat-releasing medium through radiation heat transfer is called a radiation heating surface, usually arranged in the furnace. The heating surface that mainly absorbs heat from the heat-releasing medium through convective heat transfer is called a convective heating surface, typically arranged in the flue duct after the furnace exit, in the lower-temperature smoke duct. The smoke duct with convective heating surfaces is called a convective duct. The heat release from the heating surface to the heat-receiving medium is mainly through convective heat transfer. According to the sequence of water heating and vaporization processes, the heating surface can be divided into water preheating heating surface, vaporization heating surface (also called evaporation heating surface), and superheater. The water preheating heating surface is usually arranged in the low-temperature smoke gas section to recover the waste heat of exhaust gas and save fuel, commonly referred to as an economizer.
Additionally, exhaust heat can be recovered for preheating combustion air. This type of heat recovery heating surface is called an air preheater. Economizers and air preheaters are both located at the end of the boiler flue gas path, collectively known as the rear heating surface.
The heating surface can be further classified into plate-type and tube-type based on its structure. The heating surface through which smoke flows inside the tubes is called a smoke tube heating surface, while the heating surface through which water flows inside the tubes is called a water tube heating surface. The cylindrical pressure vessel accommodating water and steam and also serving as the boiler shell is called a "steam drum" or "boiler shell." The boiler with the heating surface primarily arranged inside the boiler shell is referred to as a shell boiler (formerly known as a fire tube boiler).
For internal combustion shell boilers, the furnace is located inside the shell, known as the "furnace core." The furnace core itself is the radiation heating surface. Smoke tubes arranged inside the shell constitute the convective heating surface.
For external combustion shell boilers, the furnace is located outside the shell. In this case, part of the surface of the shell (facing the fire) serves as the radiation heating surface. Smoke tubes are still arranged inside the shell. If water tube heating surfaces are also arranged inside the external furnace as radiation heating surfaces, it constitutes a water-fire tube boiler. The shell of an external combustion boiler no longer fulfills the complete function of the boiler shell because the external furnace uses the furnace wall as the shell. Boilers with water tubes predominantly serving as the heating surface and arranged in the space of the furnace wall masonry are called water tube boilers. The heating surface, together with the drum, header, and external pipes, forms the entire water-steam system.
III. Boiler Header
The header is a key component that collects and connects the arranged furnace tubes. It has the functions of distributing water supply and discharging, and it can be categorized into upper header and lower header or inlet header and outlet header based on its position.
The upper header is located at the top of the furnace tubes, collecting the water-steam mixture from the rising tube bundles and introducing it into the steam drum through pipes. Some upper headers are installed outside the furnace wall, with rows of handholes on the opposite side of the furnace tubes for cleaning the interior of the tubes.
The lower header is located at the bottom of the furnace tubes, connected to the lower drum for water supply, distributing it to the rising furnace tubes. The lower headers on both sides of the furnace grate help prevent damage or coking of the furnace wall on both sides and are known as anti-coking boxes.
The lower header has a blowdown pipe, and its end also has handholes for inspecting and cleaning the interior of the header.
Apart from the main boiler body header, other components such as the economizer and superheater also have their respective headers. Headers are generally made of large-diameter seamless steel pipes welded with two end caps. In recent years, some manufacturers have used swaged ends instead of welded end caps, providing a more rational structure.
IV. Boiler Economizer
Definition: A heating surface that utilizes low-temperature flue gas to heat the feedwater.
The economizer, located in the rear flue duct of the boiler, heats the boiler feedwater to saturated water under the pressure of the steam drum. Since it absorbs heat from relatively low-temperature flue gas, reducing the flue gas exhaust temperature, it saves energy, improves efficiency, and is thus called an economizer.
Steel pipe economizers are not subject to pressure limitations and can be used in boiling-type economizers, usually made of carbon steel pipes with an outer diameter of 32 to 51 millimeters. Sometimes, fins and ribs are added to the outer surface to improve heat transfer efficiency. Steel pipe economizers consist of horizontally arranged parallel curved tubes (commonly known as serpentine tubes). Economizers can be classified in various ways:
1. Based on the degree of feedwater heating: Non-boiling type and boiling type.
2. Based on the manufacturing material: Cast iron and steel pipe economizers. Non-boiling type economizers are mostly made of cast iron but can also be made of steel pipes, while boiling type economizers must be made of steel pipes. Cast iron economizers are mainly used in boilers with a pressure ≤2.5 MPa. When the pressure exceeds 2.5 MPa, steel pipe economizers should be used.
3. Based on the form of the device: Vertical and horizontal.
4. Based on the relative flow direction of flue gas and feedwater: Concurrent, countercurrent, and mixed flow.
Functions of the Economizer:
1. Absorbing heat from low-temperature flue gas, reducing the flue gas temperature, minimizing flue gas losses, and saving fuel.
2. Since the feedwater is preheated in the economizer before entering the steam drum, it reduces the heat absorption on the heating surface, allowing the economizer to replace some more expensive evaporative heating surfaces.
3. With the increased feedwater temperature, the wall temperature difference upon entering the steam drum is reduced, leading to a decrease in thermal stress and an extension of the steam drums service life.
Economizer Recirculation: During the startup process of the boiler (steam drum boiler), as the circulation of the steam-water pipeline has not been established, i.e., the boiler feedwater is stagnant, the economizers water remains in a non-flowing state. With the strengthening of boiler combustion and the increase in flue gas temperature, the water in the economizer is prone to vaporization, causing a locally overheated state in the economizer. To avoid this situation, a pipeline is connected from the concentrated downcomer of the steam drum to the inlet of the economizer during startup, serving as a recirculation pipeline. This keeps the water in the economizer flowing and prevents vaporization.
V. Boiler Reheater (RH)
Definition: The reheater is a heat receiving surface that reheats the exhaust steam from the high-pressure or intermediate-pressure cylinders of a steam turbine to the specified temperature in the boiler.
The reheater is essentially a type of steam superheater that re-heats low-pressure steam that has already performed work, achieving a certain temperature. The function of the reheater further enhances the thermal efficiency of the power plants cycle and keeps the steam temperature of the final-stage blades of the steam turbine within the allowable range.
Boiler Reheater Benefits:
1. Reduces the humidity of the steam, which is advantageous for protecting the turbine blades.
2. Can improve both the relative and absolute internal efficiency of the turbine.
Boiler Reheater Function: In order to improve the thermal efficiency of large power generators, an intermediate reheat cycle is widely adopted. The main steam coming out of the boiler superheater, after performing work in the high-pressure cylinder of the steam turbine, is sent to the reheater to be reheated to increase its temperature. It is then sent into the intermediate-pressure cylinder of the steam turbine to continue expanding and performing work. This is known as a single intermediate reheat cycle, which can relatively increase the cycle efficiency by 4-5%. In some large units, the exhaust steam is sent back to the boiler for heating after the intermediate-pressure cylinder, known as a double intermediate reheat cycle, which can further relatively increase the cycle efficiency by about 2%. Some experimental units even use a triple intermediate reheat cycle. The adoption of an intermediate reheat cycle complicates the thermal system, structure, and operational regulation of the boiler-steam turbine unit, leading to increased costs. Therefore, it is typically only used in power generators with a capacity of 100 megawatts or more, and usually, only a single intermediate reheat cycle is employed.
Structure and Types: The reheater consists of tubes and headers. Steam and flue gas flow inside and outside the tubes. Based on the heat transfer method, reheaters can be divided into convective and radiant types. Convective reheaters are arranged in the convective flue duct, while radiant reheaters are arranged in the furnace (similar to superheaters).
Operating Characteristics: The flow resistance of steam in the reheating system significantly affects the cycle thermal efficiency of the unit. For every 0.1 MPa increase in resistance, the cycle thermal efficiency decreases by 0.2-0.3%. Therefore, larger tube diameters (42-60 mm) and lower steam mass velocities (250-400 kg/(m²·s) or lower) are commonly used to control the resistance of the reheater body to not exceed 5-7% of its inlet steam pressure. The pressure of the reheated steam is lower than that of the main steam, resulting in poor convective heat transfer from the steam inside the tubes to the tube wall. As a result, the metal temperature of the tube wall is higher, requiring the use of high-temperature resistant steel, and even chromium-nickel austenitic steel. The temperature of the reheated steam can be adjusted (see boiler steam temperature regulation).
Protection Measures: During boiler startup and shutdown due to accidents, there is no steam flow through the reheater, or the steam flow is minimal. To prevent overheating damage to the reheater, in addition to using high-temperature alloy steel materials, protective measures should be taken. Common measures include controlling the boiler startup speed, placing the reheater in a low flue gas temperature area, and introducing main steam cooling during startup and accidents (see turbine bypass system).
VI. Heat Pipe Heat Exchanger
(I) Overview of Heat Pipes
A heat pipe is a heat transfer component with high thermal conductivity. It transfers heat by evaporating and condensing the working fluid in a fully enclosed vacuum tube shell. It has the advantages of extremely high thermal conductivity, good isothermal characteristics, the ability to arbitrarily change the heat transfer area on both sides of the hot and cold sides, long-distance heat transfer, and temperature control. The disadvantage is poor oxidation resistance and high-temperature performance, which can be addressed by installing a ceramic heat exchanger in the front.
Heat pipe heat exchangers composed of heat pipes have the advantages of high heat transfer efficiency, compact structure, low fluid resistance, and are conducive to controlling dew point corrosion. They have been widely used in metallurgy, chemical industry, refining, boilers, ceramics, transportation, light textile, machinery, and other industries as energy-saving equipment for waste heat recovery and thermal energy utilization in the process. They have achieved significant economic benefits.
(II) Classification of Heat Pipe Heat Exchangers
According to the state of the heat transfer fluid and the cooling fluid, heat pipe heat exchangers can be divided into: gas-gas type, gas-liquid type, liquid-liquid type, liquid-gas type, and liquid-vapor type. According to the structural characteristics, heat pipe heat exchangers can be divided into integral type, split type, and combination type.
(III) Main Features of Heat Pipe Heat Exchangers
1. Heat pipe heat exchangers can completely separate the hot and cold fluids by using the heat exchangers partition plate. In the operating process, the damage to a single heat pipe due to wear, corrosion, overheating, etc., does not significantly affect the operation of the heat exchanger. Heat pipe heat exchangers are highly reliable in fluid heat exchange applications involving flammable, explosive, and corrosive fluids.
2. The hot and cold fluids of the heat pipe heat exchanger flow completely separately, making it relatively easy to achieve counter-current heat exchange between the hot and cold fluids during operation. Both hot and cold fluids flow outside the pipes, and because the heat transfer coefficient of the outside flow is much higher than that of the inside flow, it is very economical for applications involving lower-grade heat recovery.
3. For fluids with a high dust content, heat pipe heat exchangers can solve the wear and ash blocking problems of the heat exchanger through structural changes and expanding the heated surface.
4. When the heat pipe heat exchanger is used for the recovery of flue gas waste heat with corrosive components, the wall temperature of the heat pipe can be adjusted by adjusting the heat transfer area of the evaporation and condensation sections, avoiding the maximum corrosion area as much as possible.
VII. Boiler Superheater (SH)
Definition: A superheater is a heat receiving surface that heats saturated steam or steam above saturation temperature to the specified superheating temperature.
A superheater is a component in a boiler that further heats steam from saturated temperature to a superheated temperature under the corresponding pressure.
(I) Introduction:
The component in the boiler that further heats steam from saturated temperature to superheated temperature is known as the superheater. Most industrial boilers do not have superheaters because many industrial production processes and facilities only require saturated steam. In power stations, locomotives, and marine boilers, superheaters are generally installed to improve the overall thermal efficiency of the steam power system. The use of superheated steam can reduce the moisture content in the turbine exhaust. The temperature of superheated steam depends on factors such as boiler pressure, evaporation capacity, the high-temperature performance of steel, and the ratio of fuel to steel. For power station boilers, the temperature is generally around 450°C for a 4 MPa boiler and 540-570°C for boilers above 10 MPa. Some power station boilers also use higher superheated steam temperatures (up to 650°C).
(II) Types and Characteristics:
Superheaters can be classified into convective, radiant, and semi-radiant types based on the heat transfer method. According to structural characteristics, they can be classified as serpentine tube type, screen type, wall type, and wall-encased type. They consist of several parallel tubes and inlet/outlet headers. The outer diameter of the tubes is generally 30-60 mm. Convective superheaters are the most commonly used, employing serpentine tubes. They have a relatively dense tube arrangement, placed in the flue gas path with a temperature between 450-1000°C, subject to transverse and longitudinal flushing by the flue gas. Heat is mainly transferred to the tubes by convection, with a portion also being radiant heat. Screen-type superheaters consist of multiple tube screens, arranged in the upper part or exit of the furnace, belonging to radiant or semi-radiant superheaters. The former absorbs radiant heat from the furnace flame, while the latter also absorbs some convective heat. In power station boilers with a pressure above 10 MPa, a combination of screen-type and serpentine tube-type superheaters is commonly used to increase heat absorption. Wall-type superheaters installed on the furnace wall are radiant superheaters but are less commonly used. Wall-encased superheaters are used in large-capacity power station boilers to form the furnace roof and wall surfaces of the convective flue, externally coated with insulating material to form a lightweight furnace wall. The diagram shows the arrangement of several superheaters. Small industrial boilers with superheaters generally only use single-stage tube-group convective superheaters to meet requirements.
(III) Performance:
Changes in boiler operating conditions, such as load fluctuations, variations in fuel, and changes in combustion conditions, affect the outlet steam temperature of the superheater. Therefore, measures are taken in power station boilers to adjust the boiler outlet steam temperature to stabilize it at the specified value.
Common methods include:
1. Directly adjusting steam temperature using spray or surface-type desuperheaters.
2. Changing the furnace outlet flue gas temperature by using a swinging burner.
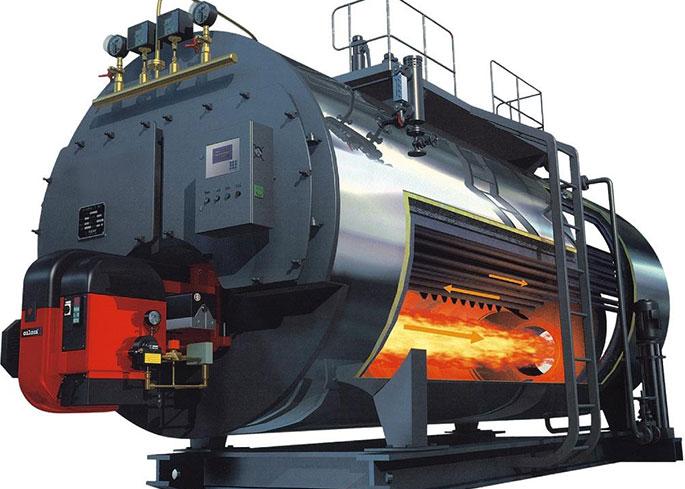
Fire tube boiler burner |