What is plate type heat transfer plate?
Plate type heat transfer plate is a multi use, can carry out welding, molding according to customer demand. Plate heat transfer plate can be made into any shape, can meet the high temperature, high pressure or corrosive environment.
The plate type heat transfer of application is as follows:
1. immersion type heating or cooling
2. external heating or cooling, heat preservation
3. device built-in heating or cooling, such as internal heating fluidized bed
4. special heat exchanger
5. evaporator, condenser
6. reaction kettle built-in, alternative coil
7. polymerization kettle cooling / heating baffle
8. ice storage
Plate type heat transfer plate characteristic
1. can provide a variety of materials
2. high operating pressure
3. high operating temperature
4. no gasket design
5. corrosion resistance
6. can be customized according to customer needs any shape
7. easy to use field cutting processing
8. efficient heat transfer type:
9. immersion type heating or cooling
10. external heating or cooling, heat preservation
11. integrated jacket type heating, cooling
12. custom heat exchanger design
13. evaporator
14. condenser
15. easy cleaning, polishing treatment
16. low pressure drop design
17. can provide pharmaceutical, food grade surface heat transfer plate
18. more heat transfer panels are used to address the special needs of users.
Type of heat transfer plate
Two sides are suppressed molding, usually for most of the use of occasions. For heating and cooling process use, the same thickness of the plate is the same as the two sides of the heat transfer plate. Can be used in stainless steel, has alloy and carbon steel, etc.. Different material and thickness to meet the work pressure.
Double side raised heat transfer plate
Only one side pressure molding, usually for a single surface, such as the tank body wall and transport bed, usually two sides of the plate is different thickness, can be used in stainless steel, has alloy and carbon steel, etc., different materials and thickness to meet the work pressure.
Single side raised heat transfer plate
In welding before using a punch punch type, in order to improve the flow channel area. Can be used in stainless steel, has alloy and carbon steel, etc.. Different material and thickness to meet the work pressure.
Application range of heat transfer plate:
1. Device built-in heating or cooling
2. The container jacket type heating, cooling or heat preservation
3. Immersion heating or cooling
4. Ice storage
5. Heat recovery board
6. Drum insulation
7. Device groove clip sleeve
8. evaporator
9. Printing and dyeing heater
10. Flue gas heat recovery board
11. The built-in concentrator or Reboiler
12. Large internal baffle plate used for cooling vegetable oil
Double plate heat transfer plate is easy to be installed in the existing storage tank and equipment, is a cost-effective method for the maintenance of temperature.
Plate type heat transfer plate Characteristic
1. easy to install in the outer wall of the storage tank and equipment.
2. to meet special shapes and dimensions.
3. manufacturing can meet the existing import and export pipeline, control system and supporting structure.
4. can provide stainless steel and carbon steel material.
5. the inherent advantages of the double side raised design is the turbulence. This design can ensure that the low flow rate can reach high turbulence, and the heat transfer efficiency is greatly improved.
6. experimental results show that the heat transfer performance of the double side raised heat transfer plate is 15% higher than that of the one side plate.
Plate type heat transfer plate used for the vast majority of heat transfer medium:
1. steam
2. hot water
3. cooling water
4. heat conduction oil
5. Heat transfer fluid
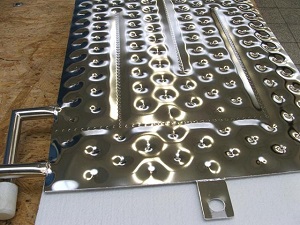
Plate type heat transfer plate |