V type serrated high frequency welding fin tubes are fins shaped in a V or zigzag pattern. This design increases the surface area of the tube, allowing for more effective heat transfer. a type of heat exchanger tubes used in various industrial applications, especially in power plants and other heat transfer systems. These tubes are designed to enhance the heat transfer efficiency between the fluid inside the tube and the surrounding environment.
The V-shaped serrated fin is a specific type of fin design used in heat exchanger tubes and other heat transfer applications. This fin design is characterized by its V-shaped profile with serrated edges, which provides several advantages for enhancing heat transfer efficiency.
The main components of the V-shaped serrated fin:
1. V-Shaped Profile: The fin is shaped like an inverted V, creating a sharp point at the top and an open base at the bottom. This V-shaped design increases the surface area of the fin exposed to the fluid or air, which improves the overall heat transfer capabilities.
2. Serrated Edges: The edges of the V-shaped fin are serrated, meaning they have small notches or teeth along their length. These serrations are intended to create turbulence in the fluid or air flow passing over the fin surface. Turbulence disrupts the boundary layer of the fluid, reducing the thickness of the stagnant layer near the fins surface and enhancing heat transfer rates.
3. High Frequency Welding: The fins are welded to the base tube using high-frequency welding techniques. This provides a strong bond between the fin and the tube, ensuring long-term durability and efficiency.
The V-shaped serrated fin Working Principle:
When the heat exchanger operates, the fluid or air flows over the V-shaped serrated fin. The fins unique geometry and serrated edges induce turbulence in the fluid flow. As a result, the fluids thermal boundary layer is constantly disturbed, which improves heat transfer by facilitating better contact between the hot or cold fluid and the fin surface.
Benefits of V-Shaped Serrated Fins:
1. Increased Heat Transfer Efficiency: The V-shaped serrated fin design significantly increases the heat transfer surface area compared to simple straight fins. The increased surface area allows for more efficient heat transfer between the fluid and the fin.
2. Enhanced Turbulence: The serrated edges promote turbulence in the fluid flow, reducing the thermal resistance and enhancing the overall heat transfer coefficient.
3. Compact Design: Due to the improved heat transfer efficiency, heat exchangers with V-shaped serrated fins can be more compact than those with traditional fin designs, making them suitable for applications with space constraints.
4. Higher Heat Transfer Rates: The combination of the V-shaped profile and serrated edges results in higher heat transfer rates, making the heat exchanger more effective at transferring heat between the hot and cold fluids.
The V-shaped serrated fin Applications:
1. Oil and Gas: In the oil and gas industry, V-shaped serrated fins are often utilized in heat exchangers for processes such as crude oil refining, natural gas processing, and petrochemical production. These heat exchangers are subjected to both high temperatures and pressures. V-shaped serrated fins help to enhance heat transfer efficiency while maintaining structural integrity under pressure.
2. Chemical Processing: Industries involved in chemical processing require efficient heat transfer equipment capable of withstanding high pressures and temperatures. V-shaped serrated fins are employed in heat exchangers and reactors for processes such as chemical synthesis, distillation, and polymerization. These fins facilitate effective heat transfer while ensuring the equipment can handle the pressure requirements of the operation.
3. Power Generation: Power plants, including thermal power plants and nuclear power plants, utilize heat exchangers and boilers to generate steam for electricity generation. V-shaped serrated fins may be incorporated into the design of these heat exchangers to improve heat transfer efficiency and withstand the high pressures and temperatures involved in steam generation processes.
4. Industrial Manufacturing: Various industries, such as automotive, aerospace, and steel manufacturing, require heat treatment processes where high temperatures and pressures are involved. V-shaped serrated fins can be found in heat exchangers, furnaces, and quenching systems used for heat treatment applications. These fins facilitate rapid and efficient heat transfer while ensuring equipment durability under pressure.
5. Food and Beverage Processing: In food and beverage processing plants, heat exchangers are used for pasteurization, sterilization, and other thermal processing operations. V-shaped serrated fins are employed in these heat exchangers to optimize heat transfer while meeting hygiene and pressure requirements.
6. HVAC Systems: Heating, ventilation, and air conditioning (HVAC) systems in commercial and industrial buildings often require heat exchangers capable of handling both high temperatures and pressures. V-shaped serrated fins may be used in air-cooled condensers, refrigeration systems, and chillers to improve heat transfer efficiency while maintaining system integrity under pressure.
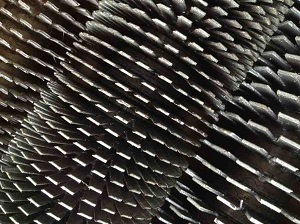
V type serrated high frequency welding fin tube |