Enhancing Heat Exchange Efficiency with Finned Tubes and Bends
Finned tubes and bends serve as indispensable components across a spectrum of industries, particularly in heat exchange systems where optimizing heat transfer is paramount. From curved finned tubes, meticulously crafted to amplify surface area and enhance heat transfer efficiency, to custom fabricated finned tubular components, including straight tubes, U-tubes, coils, and bespoke shapes tailored to diverse applications, Energy Transfer offers a comprehensive suite of solutions. Our emphasis on versatile configurations extends to various fin types, tube materials, and dimensions, ensuring tailored responses to distinct operational demands. Precision tube end formation ensures seamless integration into larger systems, guaranteeing robust sealing and optimized heat transfer performance. Through rigorous quality control measures and a commitment to excellence, Energy Transfer delivers tailored solutions engineered to meet precise customer specifications and configurations, enhancing heat exchange efficiency across industries.
1. Curved Finned Tubes:
These tubes feature fins that are precisely curved or bent to amplify surface area, thereby elevating heat transfer efficiency. Tailored to specific client specifications, considerations include material composition, dimensions, fin density, and fin material.
2. Custom Fabricated Finned Tubular Components:
Energy Transfer provides an array of fabricated finned tubular parts, encompassing straight tubes, U-tubes, coils, and bespoke shapes. Each component is meticulously crafted to suit diverse applications and industry requirements.
3. Versatile Configurations:
Our offerings underscore versatility in finned tube design and configuration. This encompasses various fin types (plain, serrated, perforated), tube materials (stainless steel, copper, aluminum), and overall dimensions, catering to distinct operational demands.
4. Precision Tube End Formation:
Seamless integration into larger systems hinges on flawless tube end connections. Tube end forming processes involve shaping tube ends to seamlessly interface with headers, manifolds, or piping systems. This guarantees robust sealing and optimized heat transfer within the system.
At Energy Transfer, our expertise lies in delivering tailored solutions for heat exchange applications. We offer an extensive range of finned tubular parts meticulously engineered to meet precise customer specifications and configurations.
Manufacturing Process for U Bend Tubes:
The manufacturing journey of U-bend tubes commences with the selection of premium seamless or welded tubes, precisely cut to specified lengths. These tubes undergo bending within specialized machinery featuring mandrels and bending dies, applying hydraulic or mechanical force to achieve the U-shape with predefined bend angles and radii. Additional heat treatment processes, such as annealing or stress relieving, may be employed to fortify material properties.
Following bending, U-bend tubes undergo meticulous trimming, deburring, cleaning, and stringent inspection to uphold dimensional accuracy and quality standards. Surface finishing treatments like polishing, pickling, or coating may be applied as per requirements. Ultimately, the finished U-bend tubes are meticulously packaged and dispatched to clients or downstream manufacturers for seamless integration into diverse industrial systems. Throughout the manufacturing process, stringent quality control measures are implemented to ensure the integrity and performance of the U-bend tubes, underscoring our unwavering commitment to excellence.
Finned Tubes and Bends Samples Inquiry
For the specified finned tubes and bends, Energy Transfer ensures meticulous adherence to quality standards and precise customization to meet project requirements. With 74 off FINNED TUBE 51 OD x 3.2WT EN10216-2-16Mo3/ASTM A240-409 and another 74 off FINNED TUBE 51 OD x 3.2WT EN10216-2-16Mo3/ASTM A36, all supplied complete with material test certificates per EN10204 3.1 and stencilled with heat numbers, we guarantee top-tier quality and traceability. The fins, Spiral Fusion Welded at 85 OD x 1.6THK x 15mm pitch, optimize heat transfer efficiency. Additionally, all tubes are precisely cut to length, with ends weld prepared, ensuring seamless integration into systems. Furthermore, the 37 off RETURN END OUTER BEND, 37 off RETURN END INNER BEND, 74 off HEADER INNER BEND, and 74 off HEADER OUTER BEND, all at 51 OD x 3.2WT EN10216-2-16Mo3, undergo stringent quality checks, including material test certificates per EN10204 3.1 and stencilling with heat numbers. The Return End Inner Bends are normalized post-bending, with signed Time-Temperature Charts and calibration certificates provided for verification. Mandrel cold bending ensures precision, while maintaining Wall Thinning at 10% maximum and Ovality at 17% maximum. Ultrasonic thickness tests and dimensional reports are supplied as proof of compliance, reaffirming our commitment to delivering tailored, high-quality solutions for heat exchange systems.
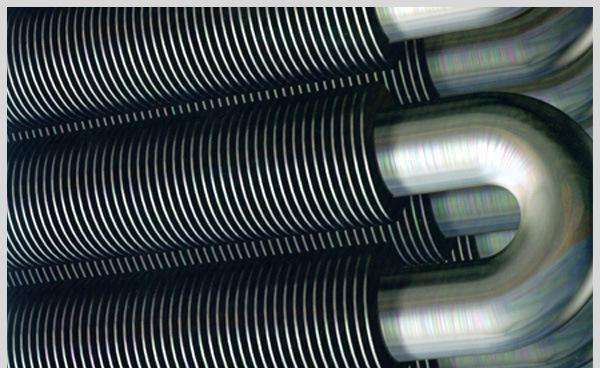
Finned Tubes and Bends |