Whats the helically wound serrated and continuously welded finned tube defination?
A helically wound serrated and continuously welded finned tube is a heat transfer surface that consists of a base tube with fins wound in a helical pattern around its outer surface. The fins have serrations or teeth along their edges, and they are continuously welded to the base tube.
How to produce helically wound serrated and continuously welded finned tube?
1. Base tube preparation: A seamless or welded tube is selected as the base tube material, typically made of carbon steel, stainless steel, or other suitable alloys. The tube is cleaned and inspected for any defects.
2. Fin preparation: The fins are typically made of a separate strip of material, often aluminum or steel. The strip is serrated along its edges to create teeth that promote turbulence and enhance heat transfer. The serrated fin strip is then cut to the desired length.
3. Helical winding: The serrated fin strip is helically wound around the base tube. This can be done using automated machinery that feeds the fin strip onto the rotating base tube, ensuring a precise and uniform winding pitch.
4. Continuous welding: As the fins are wound around the base tube, they are continuously welded to the tubes surface. This welding process ensures a strong and durable bond between the fins and the tube.
The advantages of helically wound serrated and continuously welded finned tubes include:
1. Enhanced heat transfer: The helical winding and serrated design increase the surface area of the tube, improving heat transfer efficiency and performance.
2. Mechanical strength: The continuous welding of the fins provides excellent mechanical strength, allowing the finned tube to withstand high-pressure and high-temperature applications.
3. Compact design: The helical winding allows for a higher fin density within a limited space, enabling more efficient heat transfer while maintaining compact equipment size.
4. Reduced air-side pressure drop: The serrations on the fins disrupt the airflow, creating turbulence and reducing the pressure drop on the air side, which is advantageous for air-cooled heat exchangers.
Helically wound serrated and continuously welded finned tubes application:
- Heat exchangers: Used for efficient heat transfer between fluids in applications such as oil and gas processing, power generation, and chemical processing.
- Air-cooled heat exchangers: Employed in industries where cooling using ambient air is required, such as power plants, refineries, and HVAC systems.
- Heat recovery systems: Utilized to recover waste heat and transfer it to a different medium for energy conservation.
- Refrigeration and air conditioning: Used in condensers and evaporators for efficient heat transfer between refrigerants and air.
It is important to consult with manufacturers or suppliers to ensure the specific design and specifications of helically wound serrated and continuously welded finned tubes meet the requirements of your application.
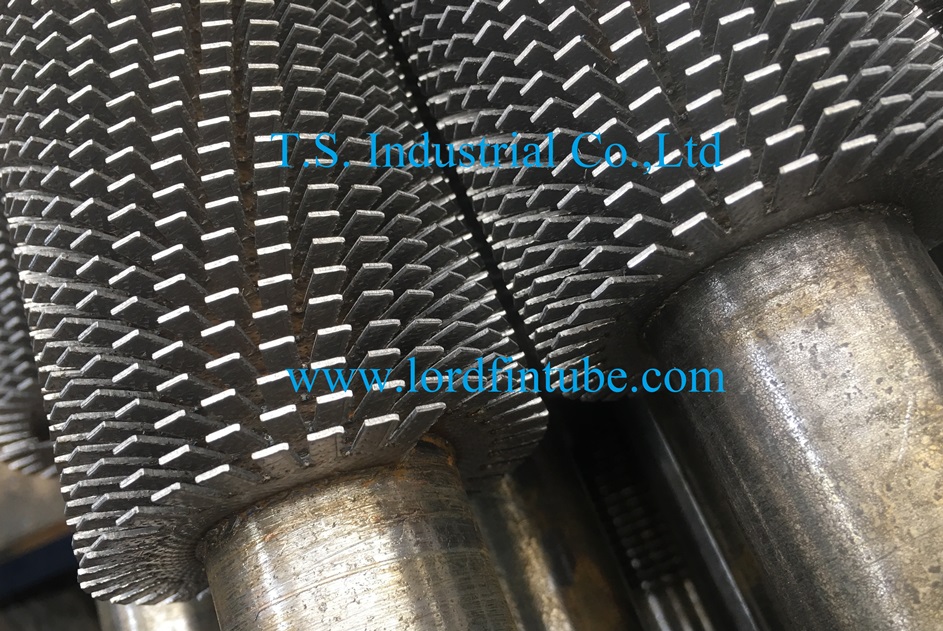
Helically wound serrated and continuously welded finned tubes |