Lord Fin Tube-SA179 aluminum 1100 L fin tube
SA179 Aluminum 1100 L Fin Tube
Advanced heat transfer solution combining carbon steel efficiency with aluminum conductivity
Product Definition
An SA179 base tube with aluminum 1100 fins in an L-type configuration refers to a specific type of heat exchanger component designed for optimal thermal transfer. This combination leverages the structural strength of carbon steel and the thermal conductivity of aluminum for superior performance.
SA179 Base Tube
- Seamless cold-drawn low-carbon steel tubes
- Excellent thermal conductivity
- Superior mechanical properties
- Ideal for heat transfer applications
- High pressure resistance
Aluminum 1100 Fins
- High-purity aluminum (99.0% minimum)
- Excellent thermal conductivity
- Lightweight and corrosion resistant
- Cost-effective solution
- Easy to form and weld
L-Type Configuration
- Fins shaped like "L" from side view
- Vertical part attached to tube surface
- Horizontal part extends outward
- Maximizes surface area for heat transfer
- Enhances turbulence for better efficiency
The purpose of combining an SA179 base tube with aluminum 1100 fins in an L-type configuration is to create a heat exchanger that can efficiently transfer heat between two fluids. When hot fluid flows through the base tube, heat is conducted through the tube wall and transferred to the attached aluminum fins. The extended surface area of the fins allows for a more effective exchange of heat with the surrounding environment or another fluid flowing over the fins.
Air-Cooled Condensers
Efficient heat dissipation in industrial cooling systems
Radiators
Thermal regulation in automotive and industrial equipment
HVAC Systems
Heating, ventilation and air conditioning applications
Industrial Heat Exchangers
Process heating and cooling in manufacturing
Design Advantage: The L-fin configuration creates turbulent flow around the fins, disrupting boundary layers and significantly enhancing heat transfer coefficients. This design can improve thermal efficiency by up to 40% compared to smooth tubes.
Base Tube Material | ||||
Fin Material | Tube Length (mm) | Fin length (mm) | Fin Tube Quantity (Pc) | Fin Material |
ASTM A210 A1 | Aluminum 1100 | 9144 | 9044 | 580 |
Base Tube O.D | Base Tube Thickness | Fin Height (mm) | Fin Thickness (mm) | Fin Pitch |
1" | BWG10 | 15.88 | 0.4 | 394FPM |
ASME SA179 Specification: Covers minimum-wall-thickness, seamless cold-drawn low-carbon steel tubes for tubular heat exchangers, condensers, and similar heat transfer apparatus. The specific dimensions, arrangement, and other design parameters of the heat exchanger will depend on the application and heat transfer requirements. Engineers consider factors like flow rates, temperature differences, pressure drops, and material properties to optimize the heat exchangers performance for a given application. |
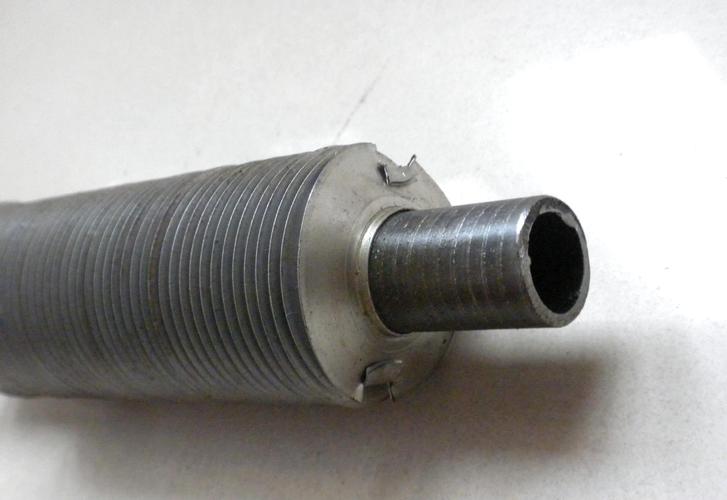
Performance Insight: The combination of carbon steel (SA179) for structural integrity and aluminum (1100) for thermal conductivity creates an optimal balance. Aluminums thermal conductivity (235 W/m·K) is approximately 5 times higher than carbon steel (45 W/m·K), making it ideal for fin applications where rapid heat dissipation is critical.