Tubesheet Type for Feedwater Heater
2024-06-09Leave a message
In feedwater heaters, tubesheets are crucial components, and their types vary based on specific application needs. The most common types include fixed tubesheets, floating head tubesheets, and U-tube bundles. Fixed tubesheets are simple and cost-effective but are limited in handling differential thermal expansion. Floating head tubesheets accommodate significant thermal expansion, reducing stress on the tubes and shell but are more complex and costly. U-tube bundles are compact, ideal for space-constrained environments, and provide efficient heat transfer, although they are more challenging to clean and maintain.
Tubesheets Type for Feedwater Heaters
1. Fixed Tubesheet with Integral Expansion Joints:
Design: The tubes are rigidly attached to the tubesheets at both ends, but the system includes integral expansion joints to accommodate thermal expansion.
Application: Used in highpressure and hightemperature applications where differential thermal expansion is a concern.
Advantage: Provides a solution for thermal expansion while maintaining a fixed connection.
Disadvantage: Integral expansion joints add complexity and cost to the design.
2. Floating Tubesheet:
Design: One tubesheet is fixed, and the other is free to move, with bellows to accommodate expansion and contraction.
Application: Suitable for applications with significant temperature fluctuations and thermal expansion.
Advantage: Reduces thermal stress on tubes and tubesheets.
Disadvantage: Bellows can be prone to fatigue and require careful design to ensure longevity.
3. U Tube Bundle with Dual Tubesheets:
Design: U tubes are supported by dual tubesheets, allowing for one fixed and one floating arrangement.
Application: Often used in horizontal feedwater heaters where space constraints are an issue.
Advantage: Allows for easy maintenance and cleaning, as well as accommodating thermal expansion.
Disadvantage: More complex manufacturing process and higher initial cost.
4. Sectional Tubesheet:
Design: The tubesheet is divided into sections, with each section independently supported to allow for differential expansion.
Application: Used in large feedwater heaters with varying thermal gradients.
Advantage: Reduces stress and potential for leakage between sections.
Disadvantage: Complex design and manufacturing process.
5. Removable Tube Bundle with Floating Tubesheet:
Design: The entire tube bundle, including the floating tubesheet, can be removed for maintenance.
Application: Ideal for applications requiring frequent inspection and cleaning.
Advantage: Facilitates easy maintenance and prolongs the service life of the feedwater heater.
Disadvantage: Higher cost due to the complexity of the removable design.
Detailed Considerations for Tubesheet Design
1. Thermal Expansion Calculation:
Accurate calculations are essential to determine the amount of expansion and contraction that will occur during operation. This ensures the selected tubesheet type can handle these changes without inducing excessive stress.
2. Material Compatibility:
The material of the tubesheet must be compatible with both the tubes and the shell to prevent galvanic corrosion. Common materials include stainless steel, carbon steel, and copper alloys.
3. Welding Techniques:
Highfrequency welding or electron beam welding is often used to attach tubes to tubesheets. The choice of welding technique affects the strength and durability of the joint.
4. Corrosion Allowance:
Additional material thickness is often included in the tubesheet design to account for expected corrosion over the equipment’s lifespan.
5. Inspection and Maintenance Accessibility:
The design should allow for easy access for nondestructive testing (NDT) methods, such as ultrasonic testing or eddy current testing, to detect potential issues early.
Example: High Pressure Feedwater Heater Tubesheet
For a highpressure feedwater heater operating at 3000 psi and temperatures up to 600°F:
Type: Fixed tubesheet with integral expansion joints.
Material: Inconelclad carbon steel for corrosion resistance and strength.
Welding: Highfrequency welding for attaching the tubes.
Design Features: Integral expansion joints to accommodate thermal expansion, thickened sections for mechanical strength, and corrosion allowance of 3 mm.
Feedwater heaters use various tubesheet types to accommodate different operational requirements. Fixed tubesheets are simple and cost-effective but limited in handling thermal expansion. Floating head tubesheets allow for significant thermal expansion, reducing stress but are more complex and costly. U-tube bundles are compact and efficient in heat transfer, suitable for space-constrained areas, though maintenance is challenging. The selection depends on factors such as operating pressure, temperature, and maintenance needs, with advanced designs featuring integral expansion joints and corrosion-resistant materials to enhance durability and performance.
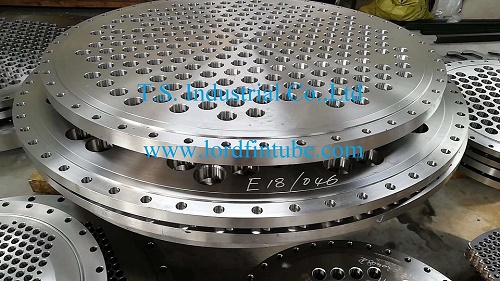