Knowledge of corrosion protection of tube sheet
Why tube sheet need protection from corrosion?
During the production of shell and tube heat exchangers, manual arc welding is used to join the tube plate and tubes, resulting in varying degrees of defects such as depressions, porosity, and slag. Additionally, force distribution on the weld is often uneven. The tube plate is typically exposed to industrial cooling water, which contains impurities such as salt, gas, and microorganisms that can cause electrochemical corrosion of both the plate and weld. The concentration of chloride and oxygen in the cooling water plays a significant role in the corrosion of the metal, as well as the complexity of the metal structure, which affects the corrosion morphology. Pitting corrosion and crevice corrosion are the primary types of corrosion that occur on the tube sheet and tube weld, resulting in corrosion products and surface pitting. Galvanic corrosion can occur when sea water is used as a medium. Chemical corrosion is also a concern when the heat exchanger tube plate comes into contact with various chemical media. Additionally, double metal corrosion can occur between the tube plate and heat exchange tube. Some tube sheets continue to erode from the medium of corrosion, and fixed tube plate heat exchangers are particularly susceptible to leakage at the connection between the tube plate and heat exchange tube due to temperature stress, resulting in failure of the heat exchanger.
In summary, the main factors that affect the corrosion of tube sheet are:
(1) the composition and concentration of the medium: the influence of concentration is different, for example, in the hydrochloric acid, the more serious the general concentration is, the more serious the corrosion is. Carbon steel and stainless steel in the concentration of 50% sulfuric acid in the most serious corrosion, and when the concentration increased to more than 60%, but the sharp decline in corrosion;
(2) impurities: harmful impurities, including chloride ions, sulfur ions, cyanide ions, ammonia ions, etc., these impurities in some cases will cause serious corrosion;
(3) temperature: corrosion is a chemical reaction, the temperature of each increase of 10 degrees Celsius, corrosion rate of about 1~3 times, but there are exceptions;
(4) pH value: the smaller the average pH value, the greater the corrosion of metal;
(5) flow rate: in the majority of cases, the greater the flow rate, the greater the corrosion.
At present, the polymer composite material for corrosion protection, which has excellent adhesive properties and temperature resistance, chemical corrosion resistance, the material is 100% solid, no volatile substances, can be used safely in a closed environment and not shrink, especially good corrosion resistance and excellent corrosion resistance of the material, the corrosion leakage of the repair parts, can provide a long-term protective coating.
Tube sheet protection operation process:
1, tools and equipment: drill sandblasting equipment, the protection of canvas or plastic, cork, alcohol or acetone, scraper, a spiral device, garbage bags, flashlight, power supply, rubber gloves, safety helmet, protective glasses, rags, brushes.
2, steps
Step 1: open the condenser end cap
With hair dryer and blower to dry the pipe surface and inside the water and with a cork plug nozzle and shelter the flanging, to ensure that the sandblasting processing does not damage the nozzle.
Step 2: sandblasting, sandblasting with canvas and other sheltered me, lest ejective sand dirty other devices. When the use of quartz sand blasting sand, it can produce 4 of the surface of the ear and will not produce more dust, to always play the base metal character. After blasting, the cork will be taken out.
Step 3p: solution cleaning: the metal surface impurities and oil cleaning.
Step 4: coated materials: first, polymer repair materials metal repairing material for the condenser tube plate and the inner wall of the pit sites were filled to avoid the water vortex, until it reaches the requirements plane as the standard. Then the polymer fluid protection material is applied evenly to the whole surface. Especially pay attention to the joint of the panel and the pipe to achieve the purpose of sealing and plugging.
Step 5: curing: in accordance with the curing requirements of the material to be cured, after curing can be put into production operation.
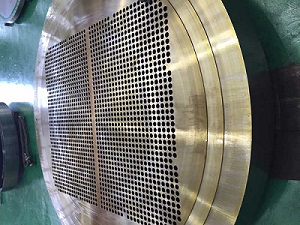