Products Description
Fixed tube sheet heat exchanger
A fixed tube sheet heat exchanger is a type of heat exchanger composed mainly of components such as a shell, tube sheet, tube bundle, and head cover (also known as the end cap). The tube sheets at both ends of the fixed tube sheet heat exchanger are welded to the shell for fixed connection. The heat exchange tubes can be either smooth tubes or low-fin tubes. Its structure is simple, manufacturing cost is low, it allows for a smaller shell diameter, and the tube bundle can be divided into various sections. The shell side can also be divided into multiple sections using longitudinal baffles, making it widely used in engineering applications.
Table of Contents
1. Structure of Fixed Tube Sheet Heat Exchanger
2. Expansion Joints of Fixed Tube Sheet Heat Exchanger
3. Number of Tube Passes in Fixed Tube Sheet Heat Exchanger
4. Main Features of Fixed Tube Sheet Heat Exchanger
Structure of Fixed Tube Sheet Heat Exchanger
Figure 1 illustrates a typical structure of a fixed tube sheet heat exchanger. As shown in Figure 1, the tube sheet of the fixed tube sheet heat exchanger is welded to the shell, and the tube sheet cannot be disassembled from the shell. The advantage of this type of heat exchanger is its relatively simple and compact structure, low cost, and widespread application. However, its drawback is that mechanical cleaning of the tube exterior is not feasible, requiring the shell side fluid to be clean, resistant to scaling, or not prone to corroding the shell. The temperature difference between the hot and cold fluids inside and outside the tubes causes thermal expansion difference, resulting in thermal stress. This stress, known as thermal differential stress, may lead to leakage at tube-to-tube sheet joints or even detachment of tubes from the tube sheet, damaging the entire heat exchanger.
Expansion Joints of Fixed Tube Sheet Heat Exchanger
The characteristic of expansion joints compensating for thermal differential stress is their simple structure. When a single wave expansion joints compensating capacity is insufficient, multiple wave expansion joints can be used. However, the number of waves in the expansion joint should not exceed 6. To provide good elasticity, stainless steel thin plates with a thickness of 1-3mm are commonly used in manufacturing. In high-pressure situations, a bellows-type expansion joint (with a protective cover) is often employed, as shown in Figure 2.
The protective cover not only allows the expansion joint to withstand higher pressure but also prevents lateral deformation, restricting the expansion joint from bending during pressurization and avoiding failure.
In general, fixed tube sheet heat exchangers with expansion joints should be used when the temperature difference between the tube wall and shell wall is below 60-70°C, and the shell side fluid pressure is not high. When the shell side pressure exceeds 0.6 MPa, considerations for higher pressure may lead to thicker bellows walls, reducing elasticity and, consequently, diminishing the effectiveness of thermal differential compensation. In such cases, other types of heat exchangers, such as floating head heat exchangers, may be more suitable.
Number of Tube Passes in Fixed Tube Sheet Heat Exchanger
Fixed tube sheet heat exchangers come in two structural types: single tube pass and multiple tube passes. In multiple tube pass heat exchangers, baffles are installed in the tube box at one or both ends of the heat exchanger, allowing the fluid to flow through only one set of heat exchange tubes at a time, exiting the heat exchanger at the end. Each set of heat exchange tubes that the fluid flows through is called a tube pass. The total number of sets of heat exchange tubes is referred to as the number of tube passes. For even numbers of tube passes, both the inlet and outlet of the tube pass fluid are installed at the same end of the heat exchanger, as shown in Figure 3. For odd numbers of tube passes, the inlet and outlet of the tube pass fluid are installed at opposite ends of the heat exchanger, as shown in Figure 4.
Heat exchangers with an even number of tube passes are generally more convenient for manufacturing, operation, and maintenance, making them more widely used. Common numbers of tube passes include 2, 4, and 6. Heat exchangers with an odd number of tube passes, except for single-pass ones, are seldom used. While multiple tube passes can increase the fluid velocity inside the tubes and enhance heat transfer efficiency, they also lead to increased friction losses and local resistance losses at the inlet and outlet; the baffles occupy a larger tube surface area; and the construction is more complex, making installation, disassembly, and cleaning more challenging. Therefore, the number of tube passes should not be too high. Single tube pass fixed tube sheet heat exchangers, besides being convenient for manufacturing, operation, and maintenance, have the advantage of achieving pure countercurrent heat transfer. This means that the flow direction of the shell side fluid is opposite to that of the tube pass fluid, resulting in significantly higher heat transfer efficiency compared to other concurrent or mixed flow heat exchangers. Therefore, the unique characteristics of single tube pass fixed tube sheet heat exchangers should be considered in their design and selection.
Main Features of Fixed Tube Sheet Heat Exchanger
A fixed tube sheet heat exchanger primarily consists of components such as a shell, tube sheet, tube bundle, and head cover (end cap). Within the circular shell, parallel tube bundles are installed, with the tube bundle ends fixed to the tube sheet using welding or expansion methods. The two tube sheets are directly welded to the outer shell, and the head cover with the inlet or outlet pipes is connected to the ends of the shell with bolts. Its characteristics include a simple structure, no shell-side sealed connections, the ability to accommodate a maximum number of tubes with the same shell diameter, minimal bypass in the flow with baffles, and the tube bundle can be divided into any number of passes. Since the two tube sheets support each other through the tubes, the tube sheet in this type of heat exchanger is the thinnest and the cost is the lowest, making it widely used.
The disadvantage of this heat exchanger is the difficulty in cleaning the shell side and the presence of thermal differential stress. When there is a significant average temperature difference between the two fluids or when the coefficient of thermal expansion of the shell and heat exchange tube materials differs significantly, resulting in thermal stress exceeding the materials allowable stress, expansion joints need to be installed on the shell. Due to the limitations in the strength of the expansion joint, the shell side pressure cannot be too high. This type of heat exchanger is suitable for situations where the temperature difference between two media is not large, or if the temperature difference is significant, the shell side pressure is not high, and the shell side medium is clean and resistant to scaling.
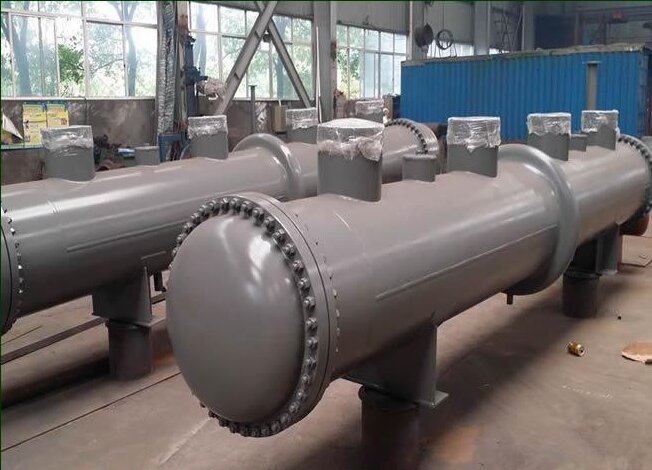