Lord Fin Tube--Immersed serpentuator heat exchanger
2015-08-22Leave a message
1. What is immersed serpentuator heat exchanger?
Introduction of immersed serpentuator heat exchanger, Heat exchanger with serpentine tube as heat transfer element, recuperative heat exchanger is one of the dividing wall type heat exchanger. This is an old type heat exchange equipment. Its structure is simple, easy to manufacture, installation, cleaning and maintenance convenient, low price, and is particularly suitable for the high pressure fluid cooling, condensation, so modern still widely used. But the large volume and heavy weight of the snake tube heat exchanger, the heat transfer efficiency is low, and the heat transfer area of the unit is high. According to the different cooling modes of the tube, the snake tube heat exchanger is divided into immersion type and spray type.
2. Immersed serpentuator heat exchanger structure
A serpentuator heat exchanger is a type of heat exchanger that utilizes a serpentine or coil-like structure to enhance heat transfer between two fluids. Its often used in various industrial applications where efficient heat exchange is crucial, such as in power plants, chemical processing, and HVAC systems.
The "immersed" aspect you mentioned could refer to the configuration where the serpentuator is fully submerged in one of the fluids being exchanged. This configuration maximizes the contact area between the two fluids, promoting efficient heat transfer.
2.1. Coil or Serpentine Tube:
This is the main component of the heat exchanger, typically made of metal such as stainless steel or copper. Its bent into a coil or serpentine shape to increase the surface area available for heat transfer.
2.2. Fluid Inlet and Outlet Ports:
These are openings at the ends of the coil where the fluids enter and exit the heat exchanger. The fluids flow through separate channels, one inside the coil and one outside (or vice versa), allowing heat transfer to occur between them.
2.3. Outer Casing or Shell:
The coil is often enclosed within a casing or shell, which provides structural support and helps contain the fluid. The casing can be made of metal or other materials compatible with the operating conditions and fluids involved.
2.4. Support Structure:
Depending on the size and weight of the heat exchanger, a support structure may be required to hold it in place and prevent sagging or deformation over time. This could include brackets, frames, or other mounting hardware.
2.5. Insulation (optional):
In some applications, insulation may be added around the outer casing to reduce heat loss or maintain a consistent temperature within the heat exchanger.
2.6. Connections and Fittings:
Various connections and fittings are used to attach the heat exchanger to the rest of the system, including pipes, valves, and flanges. These ensure proper fluid flow and facilitate maintenance and servicing.
The exact design and specifications of an immersed serpentuator heat exchanger can vary depending on factors such as the fluid properties, operating conditions, and desired heat transfer rates. Engineering considerations such as material selection, flow dynamics, and pressure drop are crucial in designing an efficient and reliable heat exchanger for a specific application.
3. Immersed serpentuator heat exchangers Advantages:
3.1. High Heat Transfer Efficiency:
The coil or serpentine design maximizes the contact area between the two fluids, resulting in efficient heat transfer. This design allows for a more compact heat exchanger with improved thermal performance.
3.2. Versatility:
Immersed serpentuator heat exchangers can be designed to handle a wide range of fluid types, temperatures, and flow rates. They are commonly used in both liquid-to-liquid and liquid-to-gas heat exchange applications.
3.3. Compact Design:
The coil or serpentine configuration allows for a high surface area to volume ratio, leading to a compact design. This is advantageous in applications where space is limited or where a smaller footprint is desired.
3.4. Reduced Fouling:
The turbulent flow induced by the serpentine structure helps reduce fouling on the heat transfer surfaces. This can lead to longer intervals between cleaning and maintenance, resulting in lower operating costs.
3.5. Enhanced Mixing:
The serpentine flow path promotes mixing of the fluids, which can help improve heat transfer performance and reduce the formation of temperature gradients within the heat exchanger.
4. Immersed serpentuator heat exchangers Disadvantages:
4.1. Complex Manufacturing:
The fabrication of the coil or serpentine structure can be more complex compared to straight tube heat exchangers. This may result in higher manufacturing costs and longer lead times.
4.2. Potential for Flow Maldistribution:
Improper design or installation can lead to flow maldistribution within the coil, which can negatively impact heat transfer efficiency and performance.
4.3. Limited to Clean Fluids:
Immersed serpentuator heat exchangers may not be suitable for applications involving fluids with high levels of particulate or fouling potential. In such cases, frequent cleaning or maintenance may be required to prevent performance degradation.
4.4. Pressure Drop:
The convoluted flow path of the serpentine structure can result in higher pressure drops compared to straight tube heat exchangers. This may necessitate the use of larger pumps or higher operating pressures to overcome these losses.
4.5. Difficulty in Inspection and Maintenance:
The compact design and intricate flow path of immersed serpentuator heat exchangers can make inspection and maintenance challenging. Access to internal surfaces for cleaning or repairs may be limited, requiring specialized equipment or procedures.
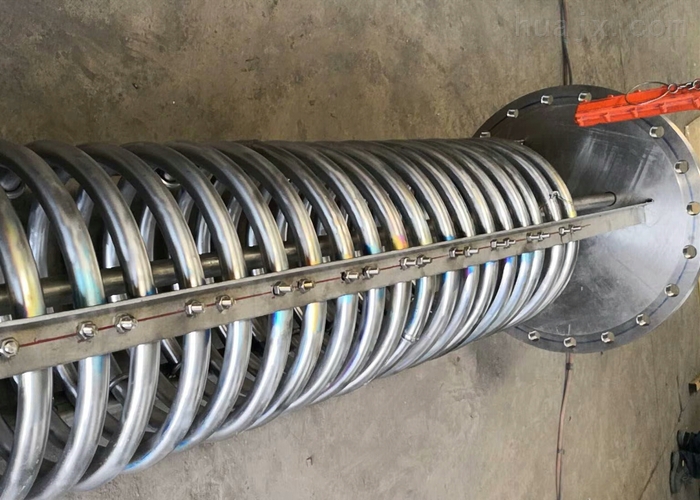