How to Selection of Fins for Steam Heat Exchangers?
2023-12-31Leave a message
How to Selection of Fins for Steam Heat Exchangers?
Fins for steam heat exchangers are designed to enhance heat transfer efficiency. Typically, fins are added to the surface of heat exchange tubes to increase the outer (or inner) surface area, thereby improving heat transfer efficiency. This type of heat exchange tube is commonly referred to as finned tubes.
Single-Metal Steam Heat Exchanger Fins:
These fins are manufactured by rolling a single aluminum or copper tube. They possess high strength, resistance to thermal and mechanical shocks, good thermal expansion properties, and eliminate the issue of contact thermal resistance. This significantly improves the heat transfer performance of the finned tubes and provides a substantial increase in the effective heat exchange surface area. The height of fins for steam heat exchangers can range from 1 to 2 mm, suitable for steel tube diameters ranging from φ19 to φ30 mm, fin spacing between 1.2 and 2.5 mm, and materials include steel, copper, and stainless steel. Currently, our factory produces steam heat exchanger fins in two main types: aluminum fins and stainless steel fins.
Bimetallic Fins:
These fins are composed of two different metallic materials (such as steel and copper) and are cold-rolled into shape on specialized machines. This design overcomes the welding limitations of aluminum with other metals and is also known as steel-aluminum composite fins, copper-aluminum composite fins, or rolled fins. Bimetallic fins utilize the pressure resistance of the base tube and the efficient heat transfer of aluminum, highlighting the characteristics of both materials in the manufacturing process. They offer advantages not comparable to other types of finned tubes.
1. Lightweight: Aluminum has the lowest density among commonly used non-ferrous and ferrous metals, making fins manufactured with it lightweight.
2. High Heat Transfer Performance: With a thermal conductivity of approximately 211.9, aluminum is more cost-effective than silver-copper. Objects with good thermal conductivity tend to absorb and dissipate heat quickly.
3. Low Air Resistance: The smooth surface of bimetallic steam heat exchanger fins reduces air resistance. Air can easily penetrate the spaces between the fins.
4. Low Contact Thermal Resistance: Practical experience demonstrates that bimetallic fins exhibit nearly zero contact thermal resistance in working environments below 210 degrees Celsius, ensuring efficient heat transfer.
Our company can manufacture steam heat exchanger fins in different ways on the base tube, including helical, in-line, welded, and rolled fins.
Low-Thread Fins:
These are efficient heat exchange tubes formed by rolling threads on the outer surface of ordinary heat exchange tubes. Typically, low-thread fins are single-metal fins made of materials such as copper, aluminum, steel, or stainless steel. The fins are directly processed on a heat exchange tube, leaving a certain thickness for pressure bearing. The height of the fins ranges from 1.5 to 3, and the spiral distance is between 1.2 and 2.2.
High-Thread Fins:
These fins have a high fin-to-tube ratio.
Extruded (Rolled) Thread Fins:
The base tube material includes carbon steel, stainless steel, etc., while the fins are extruded aluminum tubes. These fins are formed by rolling the aluminum tubes and base tubes together on a specialized machine, outperforming welded tubes, sleeved tubes, helical tubes, and smooth tubes in all performance indicators. They are widely used in various fields such as petroleum, chemical machinery, and drying and cooling processes, offering advantages such as low thermal resistance, excellent heat transfer performance, high strength, low flow loss, strong corrosion resistance, and long service life. The base tube dimensions can range from φ16 to φ32 carbon steel or stainless steel tubes, or non-standard tubes, and the finned tube dimensions can be customized according to customer requirements. Standard dimensions include a fin height of approximately 15mm, fin thickness of 0.3 to 0.35mm, fin spacing of around 3mm, with no length limitations.
When fins are rooted on the smooth tube surface, heat will be transferred from the root of the fins to the outside as heat travels from inside the tube to the outside. Simultaneously, heat is continuously transferred to the surrounding fluid through convective heat exchange, resulting in a gradual decrease in fin temperature along the height. As the fin temperature decreases along the height, the temperature difference between the fin and the surrounding fluid gradually narrows, and the heat exchange effectiveness per unit area decreases. The higher the fins, the smaller the contribution of the increased area to heat exchange effectiveness.
For commonly used high-frequency welded finned tubes in engineering, when the fin height is 15mm, the fin efficiency is around 0.8. However, with a fin height of 20mm, the fin efficiency drops to about 0.7. This indicates that choosing a fin height of 15mm is appropriate, and caution should be exercised when selecting fin heights above 20mm due to significantly lower fin efficiency, making them generally unsuitable. For aluminum fins used in air coolers, with aluminums high thermal conductivity compared to carbon steel, a fin height increase to 22-25mm is acceptable.
Choosing a smaller pitch can effectively increase the fin-to-tube ratio. However, when selecting the pitch, caution is necessary, taking into account factors such as the nature of the flowing gas and the possibility of ash accumulation. It can be divided into three situations:
1. Severe Ash Accumulation:
In cases where ash accumulation is particularly severe, such as in the exhaust of steel mills electric furnaces, converters, and some industrial kilns with high ash content, selecting a large fin pitch, for example, above 10mm, is necessary. This should be supplemented by a reasonable ash removal design and the use of ash blowers.
2. Moderate Ash Accumulation:
In cases where ash accumulation may not be severe but still requires attention, such as in the exhaust of power plant boilers and industrial boilers, a fin pitch of around 8mm is suitable, but it should be accompanied by a design scheme with self-ash removal capabilities.
3. No or Minimal Ash Accumulation:
In situations where there is no ash accumulation or only minimal accumulation, such as the exhaust from natural gas equipment or air coolers, a fin pitch of 4-6mm is acceptable. For aluminum air coolers, the fin pitch is often around 3mm.
The choice of fin thickness mainly considers the corrosiveness and abrasion of the flowing gas. For situations with severe corrosion and abrasion, thicker fins can be selected.
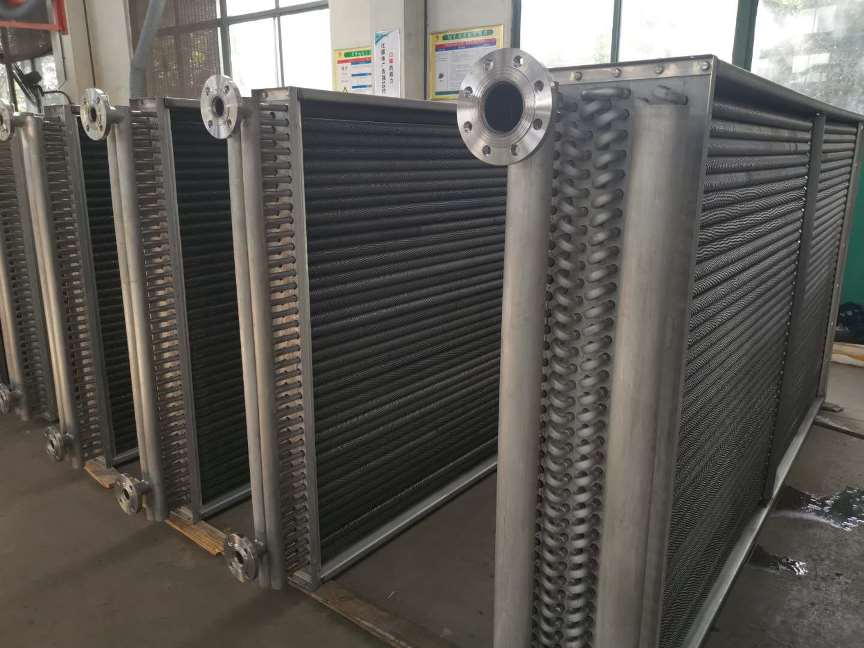