Products Description
What is Straight-Tube Heat Exchanger?
The straight-tube heat exchanger is a type of heat exchange equipment that utilizes straight pipelines for heat transfer. It is widely used in industrial applications, especially in scenarios that require efficient heat exchange, low-pressure loss, and the handling of large fluid flow rates. The design is simple and compact, yet highly flexible, allowing customization based on specific operational conditions.
Straight-Tube Heat Exchanger Operating Principle
In a straight-tube heat exchanger, hot fluid flows through the pipes, and cold fluid flows either inside the shell or around the tubes (depending on design). Heat is transferred through the pipe wall from the hot fluid to the cold fluid. The basic function of the heat exchanger is to transfer heat between two fluids with different temperatures, thus controlling their temperatures.
Straight-Tube Heat Exchanger Flow Configurations:
Parallel Flow: Hot and cold fluids flow in the same direction.
Counter-Flow: Hot and cold fluids flow in opposite directions, achieving higher heat exchange efficiency.
Cross-Flow: The fluids flow perpendicular to each other, typically used for specific process requirements.
Straight-Tube Heat Exchanger Performance Parameters
►1. Heat Exchange Efficiency
Heat exchange efficiency is a critical metric for evaluating the performance of a heat exchanger. It is influenced by factors such as pipe design, fluid velocity, and temperature difference. Straight-tube heat exchangers typically offer high thermal conductivity, making them suitable for applications with large temperature differences and high fluid flow rates.
►2. Thermal Conductivity Coefficient
The thermal conductivity coefficient measures how effectively heat is transferred through the material. The material selection for the tubes (such as stainless steel, carbon steel, copper, etc.) directly impacts the heat transfer performance. Typically, materials like copper and copper alloys are used to enhance thermal conductivity.
►3. Fluid Dynamic Performance
Pressure Loss: Straight-tube heat exchangers typically have low fluid resistance, helping reduce energy consumption. Properly designed flow paths and pipe diameters optimize fluid velocity and minimize pressure loss.
Flow Distribution: It is essential to ensure that fluid flows uniformly within the tubes to avoid localized overheating or overcooling, thereby optimizing the heat exchange efficiency.
►4. Temperature and Pressure Resistance
Straight-tube heat exchangers can be designed to withstand various temperature and pressure conditions. Different design choices and material selections ensure the exchangers stability under extreme operating conditions, such as high-temperature steam or high-pressure liquids.
Straight-Tube Heat Exchanger Structural Features
►Shell: Supports and protects the tube bundle, ensuring structural stability.
►Tube Bundle: Composed of multiple parallel tubes, responsible for the core heat exchange function. The number of tubes, tube diameter, arrangement pattern, and tube length can be customized based on specific requirements.
►Connection Ports: Inlet and outlet ports for the hot and cold fluids, typically designed for effective sealing to prevent leakage.
►Support Frame: Ensures that the tubes remain stable during operation, preventing deformation due to vibration or fluid impact.
►Material Selection: The choice of materials for the heat exchanger is critical to its performance and longevity. Common materials include:
-Carbon Steel: Suitable for applications with low temperature and corrosion levels. It is cost-effective and widely used in less demanding environments.
-Stainless Steel (such as 304, 316L): Ideal for handling corrosive fluids, offering excellent resistance to corrosion and high-temperature stability.
-Copper and Copper Alloys: Known for their excellent thermal conductivity, these materials are often used in applications requiring high heat transfer performance.
-Alloy Steel: Used in high-temperature and high-pressure environments, such as in power generation or petrochemical industries.
Straight-Tube Heat Exchanger Applications
►Chemical Industry: Used for heating, cooling, or temperature regulation in chemical reactors, particularly for managing heat during chemical reactions.
►Petrochemical Industry: Commonly used for heat exchange in the refining processes and in the management of high-temperature fluids.
►Power Generation: Employed in boiler systems, turbine systems, and cooling systems to manage heat recovery and distribution.
►HVAC Systems: Utilized in air conditioning systems, industrial cooling towers, and heat exchange applications to improve efficiency.
►Food and Beverage Industry: Used in the heating or cooling of liquids such as juices, dairy products, etc.
►HVAC (Heating, Ventilation, and Air Conditioning): Used in commercial and industrial HVAC systems for heat exchange between air and water or air and refrigerants.
Straight-Tube Heat Exchanger Advantages
►High Efficiency: Suitable for large flow rates and high-temperature differences, providing efficient heat exchange in various operating conditions.
►Design Flexibility: The heat exchanger can be customized with different sizes, tube diameters, materials, and arrangements to meet specific process requirements.
►Low Maintenance Costs: The simple design ensures ease of cleaning and maintenance, reducing downtime and operational costs.
►Reliability: High-quality materials and optimized design ensure the heat exchanger operates reliably even under harsh conditions.
Straight-Tube Heat Exchanger Case Examples
►Power Plant: A customized straight-tube heat exchanger was implemented in a power plant’s boiler system to convert high-temperature steam into heated water, significantly improving overall thermal efficiency and enabling large-scale heat recovery.
►Chemical Plant: A chemical company utilized a straight-tube heat exchanger for temperature regulation in its production process, optimizing reaction rates while reducing energy consumption.
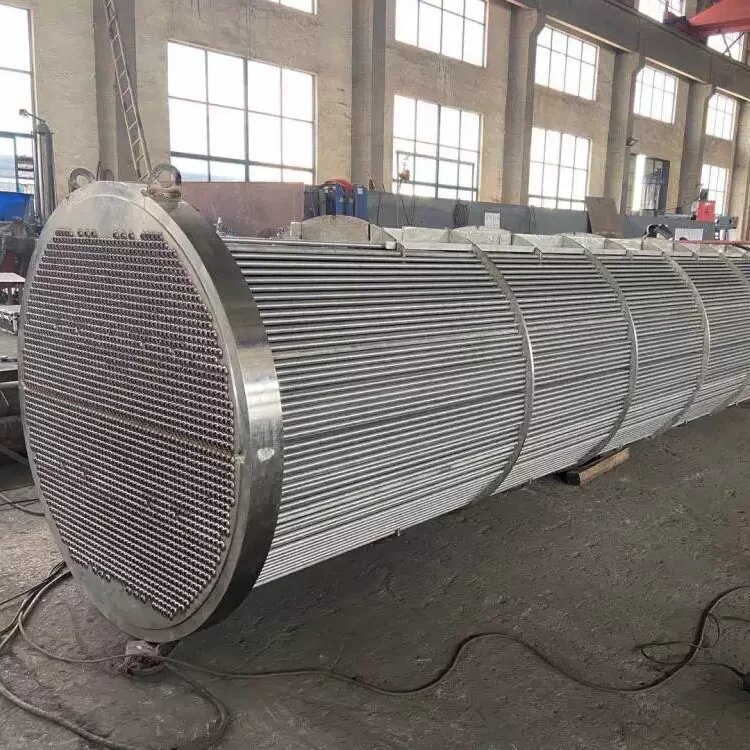