Duplex stainless steel knowledge
2024-04-06Leave a message
Detailed Explanation of Duplex Stainless Steel
Duplex Stainless Steel (DSS), with the chemical symbol S, refers to a type of stainless steel where both ferrite and austenite phases each constitute approximately 50% of the material. Generally, the lesser phase must amount to at least 30% of the stainless steel. In conditions of low carbon content, chromium (Cr) ranges between 18% to 28%, while nickel (Ni) ranges between 3% to 10%. Some steels also contain alloying elements such as molybdenum (Mo), copper (Cu), niobium (Nb), titanium (Ti), and nitrogen (N).
1. Why Doesnt Stainless Steel Rust?
The corrosion resistance of stainless steel generally increases with the increase in chromium content. When the chromium content in steel exceeds 12%, a very thin but dense oxide film (commonly known as passivation film) forms on the surface of the steel. This film protects the base metal from further oxidation or corrosion, thus providing stainless steel with excellent corrosion resistance.
2. Composition of Duplex Stainless Steel
Duplex Stainless Steel (DSS), as mentioned earlier, comprises approximately 50% ferrite and 50% austenite phases. The chromium content ranges between 18% to 28%, nickel content between 3% to 10%, and may contain other alloying elements such as molybdenum, copper, niobium, titanium, and nitrogen.
Duplex stainless steel
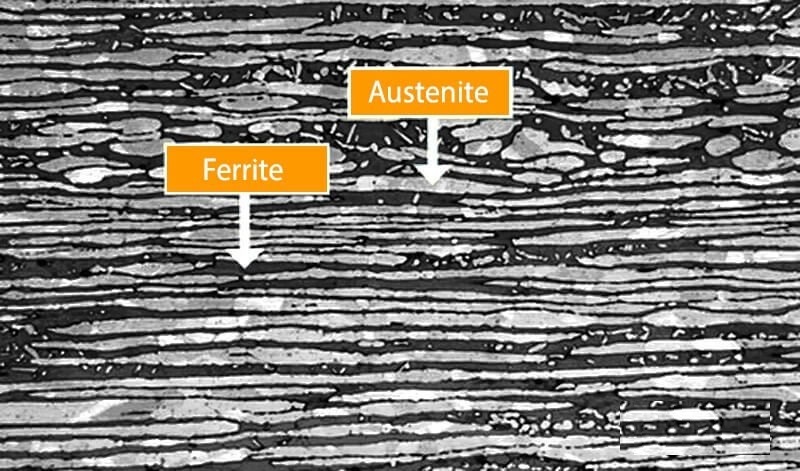
3. Classification of Duplex Stainless Steel
There are several categories of duplex stainless steel:
- Low-Alloy Type: Represented by UNS S32304 (23Cr-4Ni-0.1N), these steels do not contain molybdenum and have a PREN value of 24-25, making them suitable replacements for AISI 304 or 316 in stress corrosion applications.
- Medium-Alloy Type: Represented by UNS S31803 (22Cr-5Ni-3Mo-0.15N), with a PREN value of 32-33, these steels exhibit corrosion resistance between AISI 316L and 6%Mo+N austenitic stainless steels.
- High-Alloy Type: Typically containing 25%Cr, along with molybdenum, nitrogen, and sometimes copper and tungsten, standard grades like UNS S32550 (25Cr-6Ni-3Mo-2Cu-0.2N) have a PREN value of 38-39, offering superior corrosion resistance compared to 22%Cr duplex stainless steels.
- Super Duplex Stainless Steel Type: With high molybdenum and nitrogen content, standard grade UNS S32750 (25Cr-7Ni-3.7Mo-0.3N), and sometimes tungsten and copper, with a PREN value exceeding 40, these steels are suitable for harsh environments, exhibiting excellent corrosion and mechanical properties comparable to super austenitic stainless steels.
4. Duplex Stainless Steel vs. Austenitic & Ferritic Stainless Steel
Due to its dual-phase structure, duplex stainless steel combines the advantages of both austenitic and ferritic stainless steels. Compared to austenitic stainless steel, duplex stainless steel offers the following advantages:
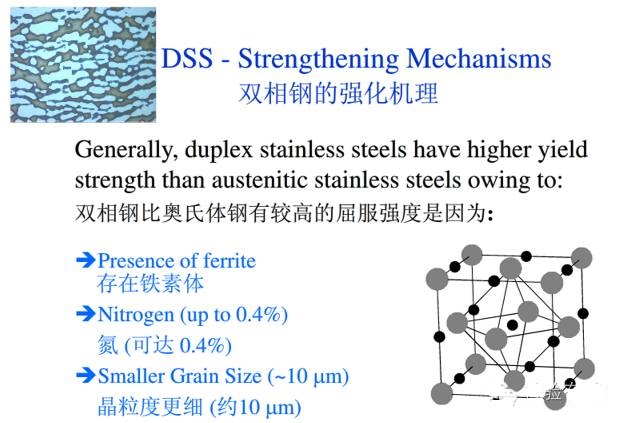
- High Yield Strength: More than double that of common austenitic stainless steel, with sufficient ductility for forming needs. Using duplex stainless steel for manufacturing tanks or pressure vessels can reduce wall thickness by 30-50%, thus lowering costs.
- Excellent Stress Corrosion Cracking Resistance: Even duplex stainless steels with the lowest alloy content exhibit higher stress corrosion cracking resistance than austenitic stainless steels, especially in chloride ion environments, addressing a significant issue in austenitic stainless steels.
- Wider Corrosion Resistance: In many media, the corrosion resistance of common 2205 duplex stainless steel is superior to that of typical 316L austenitic stainless steel, and super duplex stainless steel exhibits extremely high corrosion resistance, surpassing even high-alloy austenitic stainless steels and corrosion-resistant alloys in some media.
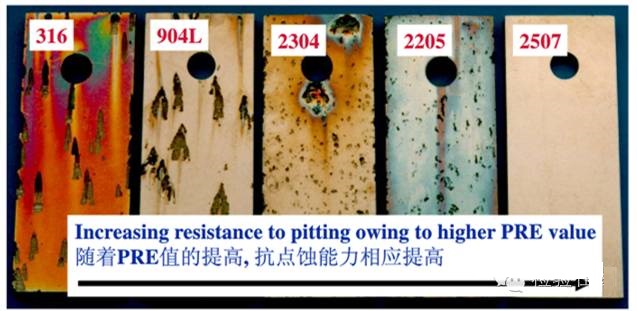
- Good Localized Corrosion Resistance: Compared to austenitic stainless steels with similar alloy content, duplex stainless steel has better resistance to wear corrosion and fatigue corrosion.
- Low Linear Expansion Coefficient: Closer to carbon steel, making it suitable for connection with carbon steel, which has significant engineering implications such as in producing composite plates or linings.
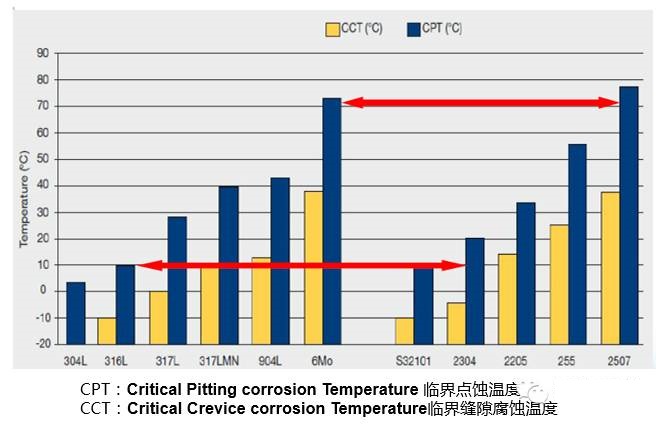
- Higher Energy Absorption Capacity: Under dynamic or static loading conditions, duplex stainless steel has a higher energy absorption capacity than austenitic stainless steel, making it advantageous for structural components to withstand sudden accidents like collisions or explosions.
However, duplex stainless steel has its weaknesses compared to austenitic stainless steel and ferritic stainless steel:
- Limited Applicability: The widespread and versatile applications of duplex stainless steel are not as extensive as those of austenitic stainless steel. For instance, its usage temperature must be controlled below 250 degrees Celsius.
- Lower Ductility: Its ductility is lower than that of austenitic stainless steel, and its cold and hot working processes and forming properties are not as good.
- Middle-Temperature Brittleness: There is a mid-temperature brittleness zone, necessitating strict control of heat treatment and welding processes to prevent harmful phase formation that could compromise performance.
In comparison to ferritic stainless steel, the advantages of duplex stainless steel include:
- Better Comprehensive Mechanical Properties: Especially in terms of ductility, it is less sensitive to brittleness than ferritic stainless steel.
- Better Localized Corrosion Resistance: Other than stress corrosion resistance, it performs better in other forms of localized corrosion compared to ferritic stainless steel.
- Superior Cold Working and Cold Forming Properties: Far better than ferritic stainless steel.
- Better Welding Performance: Also superior to ferritic stainless steel, often requiring no preheating before welding and no post-weld heat treatment.
- Wider Range of Applications: Its application range is broader compared to ferritic stainless steel.
However, duplex stainless steels disadvantages compared to ferritic stainless steel include:
- Higher Alloy Element Content: This leads to relatively higher prices, whereas ferritic stainless steel generally does not contain nickel.
5. Applications of Duplex Stainless Steel
Duplex stainless steel is a versatile material used in highly corrosive environments and structural engineering materials. Its applications include:
- Papermaking industry
- Chemical and petrochemical industry
- Hydrometallurgy
- Organic acids and caustic alkali media
- Pollution control equipment
- Chemical storage tanks
- Offshore and coastal applications
- Pipeline installations in wineries
- Building structures
6. History of Duplex Stainless Steel
Duplex stainless steel has a history of nearly 80 years, with its microstructure consisting of equal parts ferrite and austenite phases. Early grades were alloys of chromium, nickel, and molybdenum. The first batch of forged duplex stainless steel was produced in Sweden in 1930 and used in sulfuric acid papermaking industries. These steels were high-carbon duplex stainless steels, initially developed to reduce intergranular corrosion issues. In 1930, Finland produced cast duplex stainless steel, and in 1936, France obtained a patent for a steel grade later known as Uranus50. After World War II, AISI329 stainless steel became a mature grade and was widely used in nitric acid equipments heat exchanger pipelines. 3RE60 was one of the first-generation duplex stainless steel grades developed specifically to improve resistance to chloride stress corrosion cracking (SCC). Later, both forged and cast duplex stainless steel grades were used in various processing industries, including containers, heat exchangers, and pumps.
The first-generation duplex stainless steel had good performance but had limitations in the welded state. The heat-affected zone (HAZ) of the weld joint had lower toughness due to excessive ferrite, and its corrosion resistance was significantly lower than that of the base metal. These limitations restricted the application of first-generation duplex stainless steel, typically limited to non-welded applications. The invention of stainless steel refining and argon oxygen decarburization (AOD) process in 1968 made the production of a range of new stainless steel grades possible. One of the many advances brought by AOD was the deliberate addition of nitrogen as an alloying element. Nitrogen alloying of duplex stainless steel made it possible for the toughness and corrosion resistance of the HAZ to be close to that of the base metal in the welded state. As the stability of the austenite phase improved, nitrogen also reduced the rate of harmful intermetallic phase formation.
The second-generation duplex stainless steel features nitrogen alloying. This new commercial progress began in the late 1970s, coinciding with the development of North Sea offshore oil and gas fields and the demand for stainless steel with excellent resistance to chloride ion corrosion, good processing properties, and high strength. 2205 became the main grade of second-generation duplex stainless steel and was widely used in offshore oil platform gas gathering pipelines and processing facilities. Due to the high strength of such steels, allowing for reduced wall thickness and weight on platforms, their application became highly attractive.
Duplex stainless steel has been continuously evolving, with a range of grades containing different corrosion characteristics, depending on their alloy composition. Modern duplex stainless steel can be classified into five types:
- Economical duplex stainless steels without molybdenum, such as 2304;
- Standard duplex stainless steels like 2205, which are the main grades and account for over 80% of duplex steel usage;
- 25Cr duplex stainless steels like Alloy 255, with a PREN value less than 40;
- Super duplex stainless steels (PREN value 40-45), containing 25%-26% Cr, higher molybdenum, and nitrogen content than 25Cr duplex stainless steels, such as 2507;
- Hyper duplex stainless steels, high-alloyed duplex stainless steels with a PREN value exceeding 45.
7. Applications of Duplex Stainless Steel
Flue Gas Desulfurization
In coal-fired power facilities, further reducing SO2 emissions, and flue gas desulfurization (FGD) is a method to achieve low SO2 emissions. Using lime or limestone slurry to "wet scrub" SO2 from flue gas is a mature technology that has been used as a basic method in power plant boiler systems since the 1970s.
Modern FGD units can currently remove up to 90% of SO2 from exhaust gases. Modern FGD units consist of several zones with different temperatures, chloride content, and pH. Due to its lower cost and better corrosion resistance compared to austenitic stainless steel, 2205 stainless steel (S32205) has been used in FGD units in Europe and Asia. Recently, North America has also embraced the use of duplex stainless steel, making it the most popular material choice for FGD absorber tower construction due to its post-weld high strength, excellent corrosion resistance, and high toughness.
Seawater Desalination
Seawater desalination poses one of the most severe tests for materials due to its high chloride content and corrosive process environment. The history of seawater desalination is essentially the history of material development, as clients in the seawater desalination industry seek a balance between meeting corrosion resistance requirements and keeping investments within manageable limits. In early seawater desalination projects, evaporators for multi-stage flash (MSF) and multiple-effect (MED) seawater desalination plants were made of carbon steel. Later, MSF evaporators were generally clad with 316L (EN1.4404) austenitic stainless steel. MED evaporator chambers were initially coated with epoxy resin, later replaced by stainless steel cladding.
The advantage of using duplex stainless steel is its combination of high strength, twice that of traditional austenitic steels, with high corrosion resistance. Therefore, duplex stainless steel evaporators can be made with thinner steel plates and require less material and welding. Other benefits include ease of handling and less overall environmental impact.
Oil and Gas
In the oil and gas industry, duplex steel plays a crucial role in helping to withstand harsh conditions. Duplex stainless steel is mainly used in fluid pipes, process pipeline systems, and equipment such as separators, scrubbers, and pumps. Subsea, these materials are used for downhole production pipelines, fittings, manifolds, flowlines, and pipelines for transporting corrosive oil and gas. Super duplex stainless steel (25% Cr), due to its effective resistance to design stresses, is often used in various aspects such as round bars, forgings, castings, thin plates, thick plates, pipes, and fasteners.
Super duplex steel also has excellent fatigue resistance and good compatibility with other high-alloy stainless steels. Umbilicals are used for wellhead operations control using hydraulic lines and can also be used for chemical injection. Since umbilicals made of steel were introduced to the market, duplex stainless steel has been the most commonly used material. In recent years, with the trend of developing deep-sea oil and gas fields, longer umbilicals are required. Increasing the strength of the material can reduce the weight of umbilicals, allowing for longer lengths.
Biofuels
The biofuels industry, especially ethanol, is an area where the use of duplex steel is growing. 2205 stainless steel has been used in the NExBTL process equipment for biomass oil production in Singapore. In a large-scale biofuel project at the port of Amsterdam, Netherlands, tank manufacturer Oostwouder Tank & Silobouw BV used S32101 for tanks built for Noba Vetveredeling BV. In the expansion project of the Agroetanol ethanol plant on Händelö Island, Sweden, S32101 was also specified for manufacturing containers and pipelines. In many ethanol plant applications, economical duplex steel has been used to replace 300 series austenitic stainless steels.
Food and Beverage
Economical duplex stainless steel has proven its value in the food and beverage industry. This material has been applied in two projects in Spain, one for food storage tanks and the other for wine storage tanks. In the port of Barcelona, Emypro SA constructed food storage tanks entirely using S32101, replacing EN1.4301/1.4307 (304/304L). In Daimiel, southern Spain, a wine storage facility built by Spanish tank manufacturer Martinez Sole for Garcia Carrion used duplex stainless steel for the first time.
Construction Industry
Duplex steel continues to play an important role in bridge construction, where bridges are exposed to corrosion and saline environments while requiring high load-bearing strength. Two recent examples come from Asia, namely the Stonecutters Bridge in Hong Kong and the Double Helix Pedestrian Bridge in Singapore, both using 2205 duplex stainless steel. In 2006, the Stonecutters Bridge used 2000 tons of 2205 duplex steel plates and pipes, with the surface parts constructed by Chinese manufacturers using customized size plates. The plates were polished and shot-blasted to provide optimal reflectivity during both day and night.
Additionally, the Double Helix Pedestrian Bridge used 570 tons of duplex stainless steel. This bridges stunning design incorporates two helical tubular stainless steel sections resembling DNA structures, with the double helical support structures using 2205 duplex steel pipes and plates. Stainless steel surfaces provide nighttime illumination through reflected light, enhancing the design effect.
The worlds largest stainless steel roof at the New Doha International Airport in Qatar was constructed using molybdenum-containing economical duplex stainless steel (S32003). The most prominent feature of the terminal is its undulating roof, claimed to be the worlds largest stainless steel roof. The roof covers an area of approximately 195,000 square meters and used about 1600 tons of duplex stainless steel. Several factors were considered when selecting the stainless steel grade, with the most important being the airports proximity to the sea. The roof not only needs to withstand high temperatures and humidity in the Middle East but also must withstand salt corrosion. Compared to other steel grades, duplex stainless steel has cost advantages and a good strength-to-weight ratio.