What’s the process of helical tube coils?
2024-04-21Leave a message
Whats the process of helical tube coils?
Helical tube coils are manufactured through a process that involves bending straight tubes into a helical shape using specialized coiling machinery. This typically starts with selecting an appropriate material, usually metal such as stainless steel or copper, which is cut to the desired length. The tube is then fed into a coiling machine, where it is wound around a mandrel or spindle to form the helical shape. The coiling process may involve the application of heat to make the metal more pliable and reduce the risk of cracking. Once the helical shape is achieved, the coils undergo various finishing processes such as annealing (heat treatment to relieve internal stresses), cleaning, and sometimes coating to enhance corrosion resistance. The final product is a helical tube coil used in applications like heat exchangers, refrigeration systems, and fluid transfer systems, where efficient heat transfer and compact design are crucial.
1. Helical Tube Coils by Manual Bending Processing:
- Process Characteristics: Simple operation, requiring experienced craftsmen to manually operate using manual bending tools.
- Applicable Scenarios: Suitable for small-scale production, special shape requirements, such as art, decoration, etc.
- Advantages: High flexibility, strong adaptability, and can adjust shapes and sizes as required.
- Disadvantages: Low production efficiency, limited precision, and relatively high cost.
2. Helical Tube Coils by Automatic Coiling Machine Processing:
- Process Characteristics: Utilizes computer numerical control (CNC) technology to automatically complete precise bending of the coil according to pre-programmed instructions.
- Applicable Scenarios: Suitable for large-scale production, complex shape requirements, such as industrial manufacturing, construction, etc.
- Advantages: High efficiency, precision, and consistency, suitable for mass production.
- Disadvantages: High equipment investment and maintenance costs, high technical requirements for operators, not suitable for small batch production or customized projects.
3. Helical Tube Coils by Roll Bending Processing:
- Three-Roll Bending Machine:
- Process Characteristics: Bends the tube into a spiral shape through the coordinated action of three rollers.
- Applicable Scenarios: Suitable for larger diameters and thicker-walled tubes, with higher production efficiency.
- Four-Roll Bending Machine:
- Process Characteristics: Achieves higher processing precision and stability through the coordinated action of four rollers.
- Applicable Scenarios: Suitable for manufacturing spiral coils with higher precision and complex structures.
4. Helical Tube Coils by Heat Processing:
- Flame Heating:
- Process Characteristics: Softens the tube by flame heating, and then bends it using mechanical force.
- Applicable Scenarios: Suitable for larger diameters and thicker-walled tubes, but attention needs to be paid to controlling heating temperature and uniformity.
- Resistance Heating:
- Process Characteristics: Generates heat by passing current through the tube, locally heating it to soften.
- Applicable Scenarios: Suitable for cases with strict requirements for heating temperature, such as high precision and complex shape coil manufacturing.
- Medium Frequency Induction Heating:
- Process Characteristics: Locally heats the tube through the induction heating system, achieving rapid and efficient deformation of the tube.
- Applicable Scenarios: Suitable for various types of tubes, achieving efficient and precise production.
5. Helical Tube Coils by Cold Bending Processing:
- Cold Bending Machine:
- Process Characteristics: Bends the tube at room temperature without heating.
- Applicable Scenarios: Suitable for cases sensitive to temperature or requiring material performance to be maintained, but requires greater force.
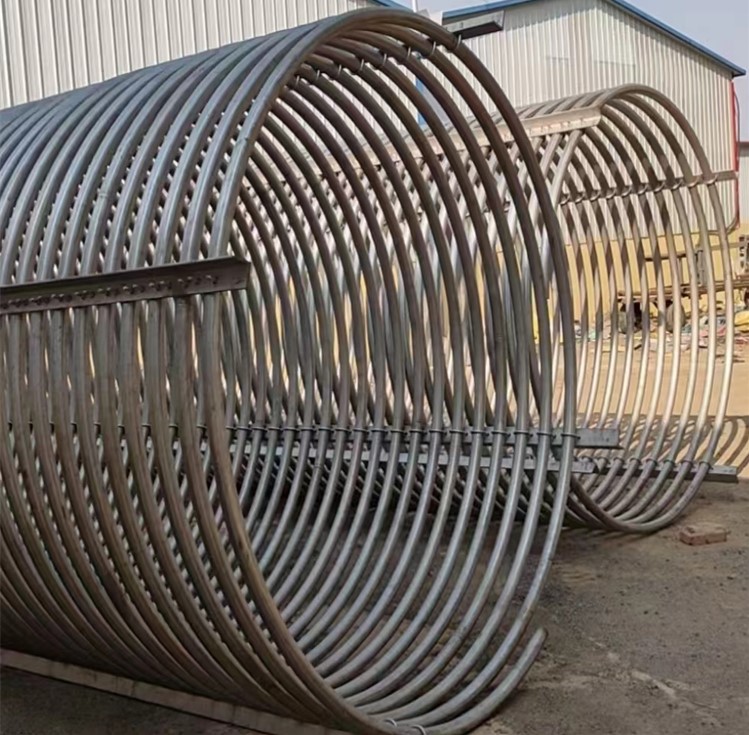