Technical requirements of H-shaped finned tube and square finned tube
H-Shaped & Square Finned Tubes
Advanced heat transfer technology with superior welding quality and performance
Technical Advantages
H-shaped finned tube or square finned tube advantages:
H-shaped finned tube or square finned tube adopts a new welding process. A number of zigzag structures are used at the welding contact parts of the fins, so that the heating is uniform, the welding surface is uniform, and the surface is smooth. There is no slag inclusion, porosity and weld beading. The welding fusion rate is up to 97%. Due to the uniform heating, the compression plastic deformation generated in the welding process is reduced, the longitudinal residual tensile stress near the weld is reduced and the residual compressive stress borne by the fin far from the weld is greatly reduced, which can significantly reduce the wave deformation of the fin and make the welding quality of H-shaped fin tube meet the requirements of technical conditions.
This innovative welding process ensures that H-shaped and square finned tubes maintain structural integrity under extreme thermal cycling conditions, making them ideal for high-performance heat exchangers in demanding industrial applications.
Technical Specifications
H Shape Finned Tube Base Tube Size | φ32*4 φ32*5 φ38*4 φ38*5 φ42*5 φ48*5 φ51*5 φ51*6 |
H Shape Finned Tube Fin Size | 70mmX70mm、75mmX75mm 和 95mm X 89mm |
H Shape Finned Tube Base Tube Material | Carbon steel, stainless steel, ND steel, alloy steel, etc. |
H Shape Finned Tube Base Fin Material | Carbon steel, stainless steel, ND steel, alloy steel, etc. |
It can be customized according to the specific requirements of users, and we can also help users design |
Our manufacturing capabilities allow for complete customization to meet specific operational requirements. Whether you need unique dimensions, specialized materials, or specific performance characteristics, we can engineer the perfect solution.
Production Technical Requirements
Welding Strength & Stability
- Pull off force test: greater than 200MPa or partial tear of steel pipe
- Weld width: greater than fin thickness, i.e. welding rate > 99%
- Stability of welding strength: the first piece of each shift shall be welded to meet the requirements
- Weld bending resistance test: fins bent 20° left/right twice with no cracks
- Hammer test: fin falls off without breaking
- If test fails, annealing function must be enabled
Heat Affected Zone
- Measurement with microscope and microhardness tester
- The depth of heat affected zone of steel pipe is less than 0.5mm
- Consistent thermal properties across all fin-tube interfaces
- Minimal structural deformation during thermal cycling
Dimensional Accuracy
- Overall length: -1mm ~ +1mm
- Spacing: -0.2mm ~ +0.2mm
- Verticality of fins and steel pipes: -1° ~ +1°
- Flatness of butt welded fins: -0.2mm ~ +0.2mm
- Height difference: -0.2mm ~ +0.2mm
- Double pipe center distance: -0.5mm ~ +0.5mm
- Consistent length change after welding
Welding Speed
- Base tube outer diameter 25~51mm
- Fin thickness 2mm
- Each pair welding time < 3s
- Excluding feeding/unloading and annealing time
- High-speed precision welding with robotic systems
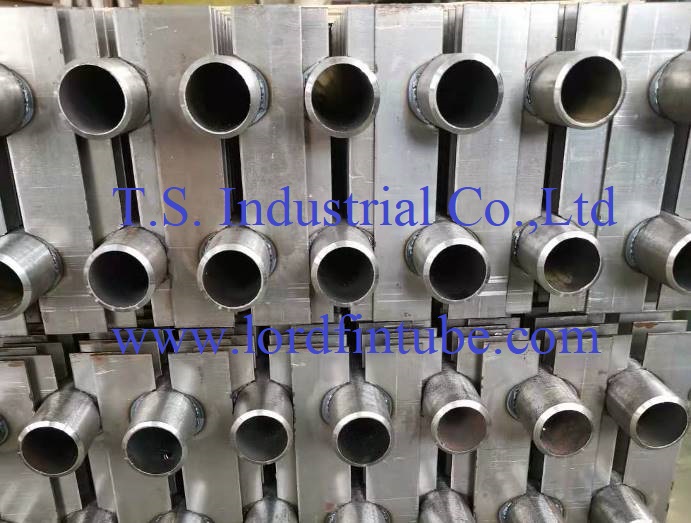
Quality Assurance: Our H-shaped and square finned tubes undergo rigorous quality control at every stage of production. From material selection to final inspection, we ensure each tube meets the highest industry standards for thermal performance, structural integrity, and longevity.