High-frequency welded finned tube
2022-09-25Leave a message
High-Frequency Welded Finned Tubes
High-frequency welded (HFW) finned tubes are advanced heat transfer components manufactured using high-frequency currents skin and proximity effects. This process simultaneously heats a steel strip and base tube surface to a plastic/melted state while winding under pressure, creating a solid-phase weld that integrates fin and tube into a unified structure.
HFW Finned Tubes Advantages
- 95%+ welding rate - Superior metallurgical bond quality
- 8x heat dissipation vs. bare tubes
- 200MPa+ tensile strength at fin-tube joint
- 1.10~1.20w/kg·℃ metal thermal strength
- 6m maximum lengths reduce connection points
- Minimal maintenance requirements
HFW Finned Tubes Technical Specifications
Construction & Materials
- Base Tubes: Stainless steel, ND steel (corrosive environments), Carbon steel (non-condensing)
- Fin Materials: Carbon steel, Corrosion-resistant steel, Stainless steel, Alloy steel
- Fin Thickness: ≥0.8mm
- Fin Height: Typically < base tube radius
- Surface Treatment: Internal/external hot-dip galvanization
Design Variants
- Solid Fin Tubes: Standard continuous fin design
- Serrated Fin Tubes: Enhanced heat transfer for high-fin applications
Performance Characteristics
- Operates in high-temperature/pressure environments
- Smooth internal bore minimizes flow resistance
- Wide operational temperature range
- Superior wear resistance
HFW Finned Tubes Industrial Applications
- Power Generation: Boiler economizers, air preheaters
- Petrochemical: Process heaters, reformers
- Metallurgy: Furnace heat recovery systems
- Water Treatment: Thermal fluid systems
- HVAC: Industrial heat exchangers
HFW Finned Tubes Comparative Benefits
Outperforms traditional methods (inlaying, brazing, hot galvanizing) in:
- Welding integrity and joint strength
- Production efficiency and automation capability
- Heat transfer efficiency per unit mass
- Long-term operational reliability
Manufacturing Process
Proprietary high-frequency welding technology bonds 0.8-1mm steel strips to base tubes through simultaneous heating and pressure application during winding. This national-patented process ensures complete fusion while maintaining dimensional precision.
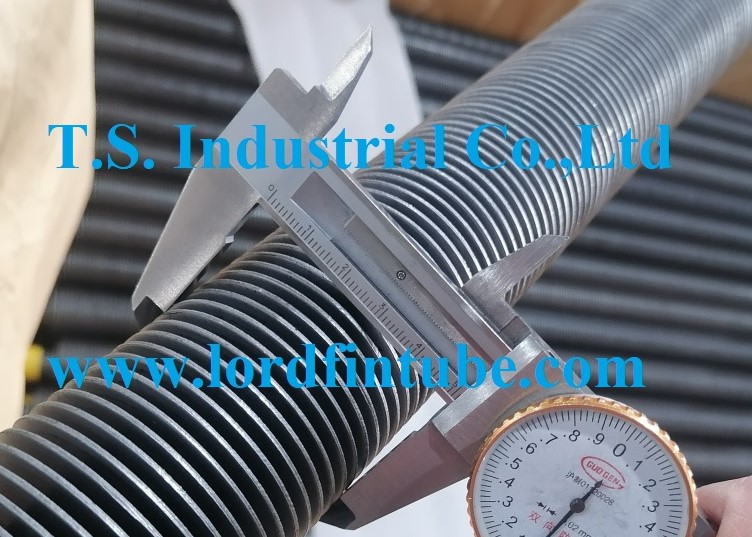