Products Description
What is Platen Superheater?
Platen Superheater, also known as full radiation superheater, refers to a type of superheater typically positioned at the upper part of the furnace or at the flue gas outlet, where it receives both direct radiant heat from the furnace and convective heat from the flue gas. Adjacent platen superheaters maintain a significant distance between them, serving to reduce the temperature of flue gas at the furnace outlet and prevent slagging on the downstream heating surfaces. It is also a primary component of modern large-scale boiler superheaters.
Alias: Full Radiation Superheater
Function: Reduce the temperature of flue gas at the furnace outlet
Classification: Vertical, Vertical Drainage, and Horizontal Platen Types
Discipline: Power Engineering
Introduction to Platen Superheater:
Platen superheaters are often horizontally arranged to save on steel consumption for support frames and to increase stability. Due to the pre-welding of individual tube screens into single pieces before leaving the factory, the front screen is usually hoisted in single pieces or in small groups. Rear screen assemblies often include primary and secondary temperature reducers and feature numerous field welds, making assembly more advantageous than single installation.
To maintain lateral spacing between tube screens and enhance stability, a protruding bow-shaped tube is often used to overlap every two tube screens. During assembly, careful inspection and adjustment of the position and dimensions of these bow-shaped tubes are necessary to ensure smooth connection and accurate positioning of each pair of tube screens in a suspended and parallel state.
Before welding the tube rows to the headers, a 35° slope with a 1:3 ratio and a gap of 1-2mm, with a blunt edge of 0.5mm, should be prepared on the tubes, with a clean-up within 10-15mm of the tube end both internally and externally. Temporary fixation of the headers should be done using methods like banding to avoid spot welding directly on the headers.
The quality requirements for assembled components are similar to those for convection superheaters. Regardless of whether platen superheaters are hoisted in single pieces or assemblies, they are relatively simple due to their smaller volume and mass. Therefore, the quality requirements are similar to those for convection superheaters.
Structure of Platen Superheater:
Platen superheaters are composed of steel tubes with outer diameters ranging from 32 to 42mm and headers, generally suspended above or located at the furnace outlet. Each screen typically contains 15 to 30 tubes, determined based on the required steam flow rate. The spacing between screens (s1) is between 500mm and 1000mm, and the ratio of the spacing between tubes within each screen (s2) to the tube diameter (s2/d) ranges from 1.1 to 1.25. Platen superheaters absorb both convective and radiant heat, with the proportion of heat absorbed at each location determined by the superheaters position.
1. Vertical Platen Superheater:
The U-shaped tubes of the platen superheater are arranged vertically, as shown in Figure 1. This vertical structure is simple and easy to support but has poor exhaust and drainage properties.
2. Horizontal Platen Superheater:
The tubes of the platen superheater are arranged horizontally, as shown in Figure 2. Its advantages and disadvantages are opposite to those of vertical platen superheaters.
3. Vertical Drainage Type Platen Superheater:
Its structure is shown in Figure 3. This type of platen superheater is characterized by convenient drainage, simpler support than horizontal types, but slightly more complex structure.
Use of Platen Superheater:
Platen Superheater Technical Parameters:
This type of superheater consists of many folded tubes installed in parallel, with wide gaps between tubes and parallel to the airflow. The inlet duct is protected by a stainless steel shell bonded with special adhesives. Heat transfer occurs via radiation rather than convection, allowing these superheaters to be installed in hotter positions where tube bundles cannot (e.g., flue gas temperatures up to 800°C during municipal waste incineration), as tube bundles are prone to blockage and corrosion. On these platen superheaters, deposits solidify when they reach a thickness of 2cm. Due to the absence of blockages, manual cleaning and related shutdowns are significantly reduced. Due to radiant heat transfer, steam temperature can remain constant for over a year without corrosion occurring during this period.
Platen Superheater Environmental Benefits:
Platen superheaters can withstand high superheated steam temperatures practically and reliably.
Platen Superheater Applicability:
Can be installed in any boiler with two or three flue gas passes.
Platen Superheater Economic Viability:
When applied in areas with high flue gas temperatures (second or third flue gas passes), it is much cheaper than using tube bundle superheaters. There may be an increase in construction costs, but this needs to be fully considered, as the use of this type of superheater may also prolong the life of the heat exchanger.
Platen Superheater Driving Force for Application:
Extended operating cycles at high superheated steam temperatures.
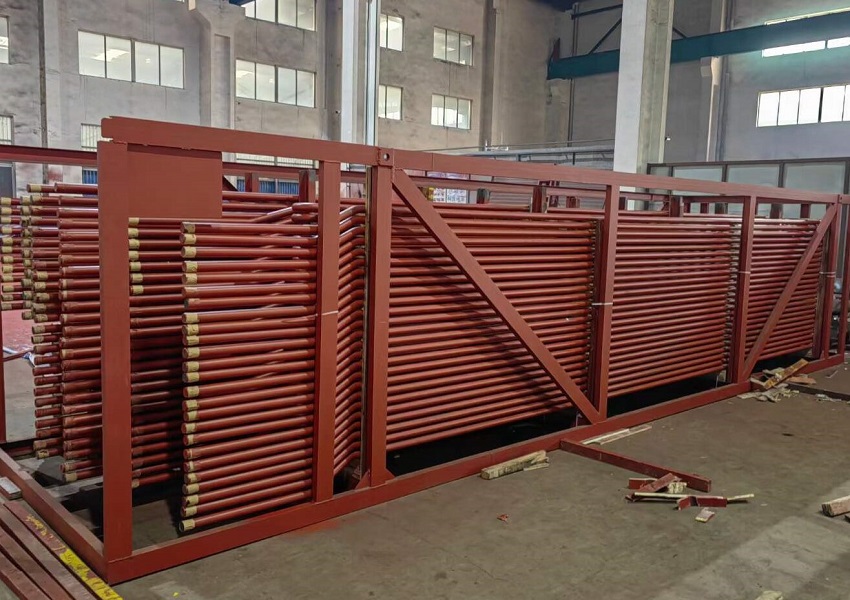