Introduce Shell and Tube Heat Exchanger Tube Sheet
2025-01-13Leave a message
The most popular type of conventional heat exchanger is the shell and tube type. In order to transmit heat between two fluids, it is primarily composed of a circular shell, heat exchange tubes, tube sheets, baffles, and tube boxes. It can function at high temperatures and high pressures and has a straightforward structure. Among other industries, it is widely utilized in the chemical, petroleum, and electrical sectors.
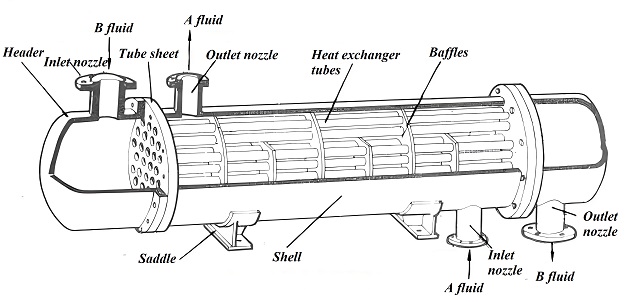
What is Tube Sheet?
The tube sheet is an indispensable part of the shell and tube heat exchanger. It is a flat and thick metal plate with several holes on it. A tube is fixed in each hole. These heat exchange tubes are usually arranged in bundles, and one or both ends of the tubes are fixed through the tube sheet, providing a fixed support structure for the tubes in the shell. The diameter and arrangement of the holes are determined according to the diameter, number, arrangement of the tubes in the tube bundle and the specific design requirements of the heat exchanger.
The tube sheet not only supports the tube bundle, but also acts as a seal to prevent fluid leakage or cross flow.
Structure of Tubesheet
✔ Pass partition groove (with chamfer; chamfer should be 45°): groove width 8mm-14mm
✔ Tube hole layout: regular triangular (30°), rotated triangular (60°), square (90°), rotated square (45°)
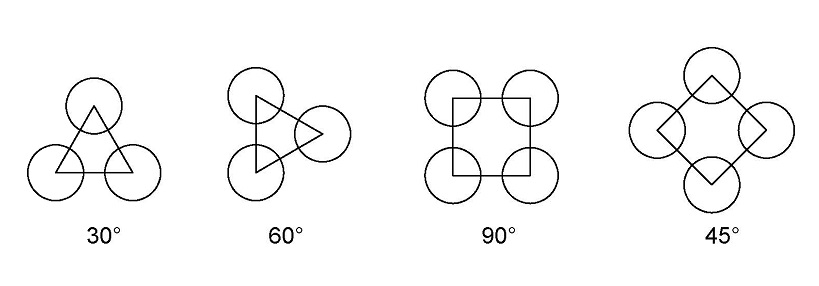
Functions
✔ Support and fix the tube bundle
The tube sheet fixes the tubes of the tube bundle in the shell, ensuring the stable operation of the tubes throughout the heat exchange process and preventing the tubes from loosening or falling off due to fluid pressure or vibration.
Each tube of the tube bundle is connected to the shell through the holes in the tube sheet, ensuring the stability of the position of the tube and the direction of fluid flow.
✔ Sealing fluids
A seal is formed between the tube sheet and the shell to prevent leakage and cross-flow of the fluid in the tube and the fluid in the shell.
✔ Separating fluids
The tube sheet acts as a barrier between the two fluids (hot and cold) circulating in the heat exchanger. One fluid flows in the tube, while the other fluid flows in the shell outside the tube. The tube sheet physically separates the fluid in the shell and the fluid in the tube to prevent them from directly mixing to maintain heat exchange and prevent cross-contamination between the fluids.
✔ Compensation for thermal expansion
In a working environment with a large temperature difference, the temperature change of the hot fluid and the cold fluid will cause the tube to expand or contract. The tube sheet needs to be designed with thermal expansion compensation in mind, especially in floating tube sheet-type heat exchangers, where one end of the tube sheet may need to float to avoid excessive stress caused by temperature difference.
Type of Shell and Tube Heat Exchanger Tube Sheet
The two ends of the tube sheet are fixed to the tube bundle, and the tube sheet is fixedly connected to the shell by welding and cannot be disassembled. It is suitable for working occasions with small temperature differences and low pressure.
Disadvantages:
- The tube sheet cannot be disassembled, so the part inside the outer shell of the tube cannot be cleaned. It can only require that the shell fluid must be clean, not easy to scale or corrode the shell.
- Because the inside and outside of the tube are two different temperatures of hot and cold fluids, the wall temperature of the tube and the shell is different, which causes a thermal expansion difference between the heat exchange tube and the shell. The shell and the tube sheet are welded, and the heat exchange tube is connected to the tube sheet. The heat exchange tube, shell, and tube sheet constrain each other, limiting the free expansion of the tube bundle.
As a result, stress will be generated on the total cross-section of the tube wall and the cross-section of the shell wall. This stress is caused by the different temperatures of the tube wall and the shell wall, so it is usually called temperature difference stress. The greater the temperature difference between the tube wall and the shell wall, the greater the temperature difference stress. Temperature difference stress may cause leakage in the joint between the tube and the tube sheet or even cause the tube to be pulled off the tube sheet, destroying the entire heat exchanger.
One end of the tube sheet is fixed to the shell, while the other end is allowed to float freely in the shell and move with the thermal expansion of the tube bundle. When the temperature difference between the two media is large, no temperature difference stress is generated between the tube bundle and the shell. It is suitable for working conditions with large temperature differences, and thermal expansion of the tube bundle needs to be compensated.
Advantages:
The floating head end is designed as a detachable structure so that the tube bundle can be easily inserted or pulled out of the shell. This provides convenience for maintenance and cleaning.
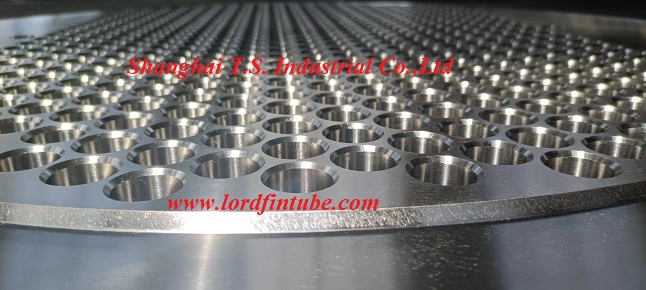
Shell and Tube Heat Exchanger Tube Sheet
Available Materials
Materials: Single material, composite materials
- Single material: stainless steel, duplex stainless steel, naval brass, titanium alloy, etc.
- Composite materials: stainless steel-alloy steel, nickel alloy-alloy steel, copper-alloy steel, etc.
Minimum Thickness of Tube Sheet
-For explosive and extremely toxic media, the minimum thickness of the tube sheet (excluding corrosion allowance) should not be less than the outer diameter (OD) of the heat exchange tube.
-For other occasions, the minimum thickness of the tube sheet is as follows:
OD≤25, mini thk≥0.75OD
25<OD<50, mini thk≥0.7OD
OD≥50, mini thk≥0.65OD
Processing Method of Shell and Tube Heat Exchanger TubeSheet
-Material: Generally a round disc, flat and without holes
-Machining:
According to the requirements of the technical drawings, a predetermined number of holes are drilled on the tube sheet by machine. The hole diameter is usually slightly larger than the outer diameter of the tube so that the tube can be smoothly inserted into the hole.
Subsequent processing:
-Deburring: The edge of the hole may have burrs or irregular cutting marks, which need to be removed by polishing, grinding, or deburring tools. This process ensures that the edge of the hole is smooth and avoids damage to the surface of the tube.
-Dimension detection: Check whether the size and position of the hole meet the design requirements to ensure that the tube can be smoothly inserted and fixed. Make fine adjustments if necessary to ensure that the tube bundle can be firmly fixed on the tube sheet.
How to connect the tube sheet to the heat exchanger tubes?
⚑ Expansion joint
It is used when leakage of medium between tube shells will not cause adverse consequences. The expansion joint structure is simple, and the tube is easy to repair.
Process:
First, put the tube expander into the tube to enlarge the diameter of the tube, plastically deform it, and fit it tightly on the tube sheet. The tube sheet in contact with the tube mouth will also enlarge as the tube mouth enlarges, thus elastically deforming.
When the tube expander is pulled out, the elastic deformation of the tube sheet will return to its previous size, but the tube mouth after plastic deformation will remain enlarged and will not return to its original state, so that the two are tightly connected together.
Due to the plastic deformation of the expansion tube end during expansion, there is residual stress. As the temperature rises, the residual stress gradually disappears, which reduces the sealing and bonding effect at the tube end. Therefore, this expansion structure is subject to certain restrictions of pressure and temperature.
Applicable pressure: ≤4 MPa
Tube hole roughness: Ra12.5
Tube hole form: The form of the tube hole is related to the expansion strength.
✔ Bright hole:
When the pull-off force on the expansion mouth is small, the bright hole can be used; it is used for heat exchangers with good material properties.
Expansion depth: tube sheet thickness -3mm; when the tube sheet thickness is greater than 50mm, the expansion depth is 50mm, and the tube end protrudes 2-3mm.
✔ Hole with annular groove: When the pull-off force is large, the structure with annular groove can be used.
Purpose: to improve the pull-off resistance and enhance the sealing performance
Structure: A small annular groove is opened in the tube hole, with a depth of 0.4-0.5 mm.
When the tube is expanded, the tube wall is squeezed into the groove to form a mortise and tenon structure. The tube is tightly connected to the tube sheet and is not easy to fall off.
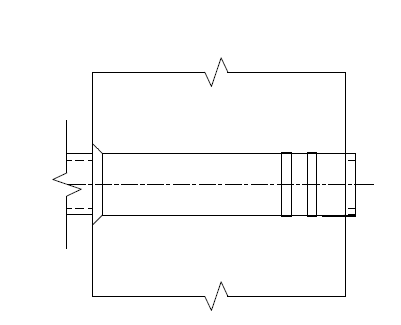
The number of grooves in the tube hole is generally determined by the thickness of the tube sheet. When the thickness of the tube sheet is less than 30mm, one groove is opened in the tube hole; when the thickness is ≥30mm, two grooves are opened.
Note: When the tube sheet is a composite material, the groove position is divided into two situations.
1.When the composite layer is thin, the groove position is on the base layer.
2.If the coating is thick, one groove can be opened on the composite layer, but it is not allowed to open the groove between the coating and the base layer.
⚑ Welding
It is widely used. Since the tube holes do not need to be grooved, and the roughness requirements of the tube holes are not high, the ends of the tubes do not need to be annealed and polished, so the manufacturing and processing are simple.
The welding structure of the tube and the tube sheet has high strength and strong pull-off resistance. When the welding part leaks, it can be repaired by welding. If the tube needs to be replaced, a special tool can be used to disassemble the welded leaking tube, which is more convenient than disassembling the expansion tube.
⚑ Expansion joint + welding
Used for media with high pressure, strong permeability, or corrosive on one side.
Process:
Expansion before welding: Expand the tube before welding to improve the fatigue resistance of the weld, because the tube wall is close to the tube plate hole wall after expansion, which can prevent cracks during welding.
Welding before expansion: The lubricating oil used for expansion can be prevented from affecting the quality of the weld, but welding before expansion may cause the weld to crack during expansion. The advantage of welding before expansion is that there is no need to clean the oil residue after expansion, but the position of the expansion tube during expansion after welding is required to be high. It must be ensured that the expansion is not performed within the range of 10 to 12 mm; otherwise, the weld is easily damaged.
Expansion after welding: Generally suitable for heat exchange equipment with higher pressure. The welding part is strengthened sealing welding, and the welding waist height is 2.8 mm. The expansion part bears the force. When the expansion fails, the strengthened sealing welding can bear the force, and the sticking expansion part is to eliminate crevice corrosion.
⚑ Inner-hole welding
After processing, the tube sheet and the heat exchange tube form a butt weld. Special equipment is required to insert the welding gun from the tube hole on the tube sheet side into the weld for welding, which optimizes the stress state at the connection between the heat exchange tube and the tube sheet and greatly reduces the edge stress. It is very practical for heat exchangers with stress corrosion or gap corrosion media.
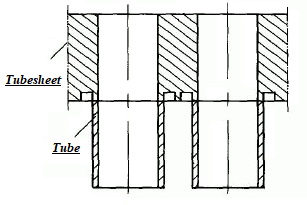
⚑ Explosive bonding
Suitable for expansion of thin-walled tubes, thick-walled small-diameter tubes, and thick tube sheets
Using explosives, the tube is deformed in a very short time under the action of high-pressure gas shock waves, so that the tube wall is firmly attached to the tube sheet hole.
Advantages:
- High connection strength
- High pull-off resistance
- Small axial elongation and deformation of the tube
- No lubricating oil is required, and there is no oil stain on the tube end, which is very beneficial for welding after expansion.
The difference between tube sheets and baffles
✔ Structure
Tube sheet: it is usually a whole circular plate with many holes drilled in it.
Baffle: it is usually arched and not a complete circle.
✔ Function
Tube sheet: mainly used to support the tubes and separate the fluid in the shell and tube
Baffle: used to change the flow path of the fluid, increase the turbulence of the fluid, and increase the heat transfer efficiency
✔ Location
Tube sheet: located at both ends of the heat exchanger
Baffle: located between the tube sheets at both ends of the heat exchanger, arranged at intervals along the length of the shell, and running through the tube array