Common Testing Techniques for Heat Exchangers
2025-01-18Leave a message
Common Testing Techniques for Heat Exchangers
(I) Visual Inspection
Visual inspection is the most basic method for testing heat exchangers. It involves checking the appearance, structure, and dimensions of the equipment visually or with simple tools to ensure they meet safety requirements.
⇒Checking the body and welds for signs of overheating, deformation, or leakage;
⇒Using a high-magnification lens to examine weld surfaces for cracks;
⇒Inspecting the foundation and supports for cracks, tilting, or sinking;
⇒Observing the inner and outer surfaces of the body for corrosion or noticeable mechanical damage.
(II) Non-Destructive Testing
Non-destructive testing (NDT) is a critical technique for assessing the structural integrity of heat exchangers. Common methods include:
⇒1. Surface Testing
Surface testing is widely used for inspecting butt welds, fillet welds, and welds between tube sheets and tubes. It helps detect surface cracks and other defects.
⇒2. Ultrasonic Testing
Ultrasonic testing can detect internal and subsurface defects in butt welds from the external surface without removing the core components. It is efficient and convenient for identifying fatigue cracks and hidden flaws.
⇒3. Radiographic Testing
Radiographic testing is primarily used to detect internal defects in butt welds of steel plates and to re-inspect any critical defects identified by ultrasonic testing. This method requires the core components to be removed beforehand, and radiation protection measures must be implemented on-site.
(III) Hydrostatic Testing
Hydrostatic testing is an essential method for evaluating the strength and sealing performance of heat exchangers, especially for pressure tests.
⇒Testing Principle: Water is injected into the heat exchanger, and pressure is applied to assess its pressure resistance and sealing performance.
⇒Testing Procedure:
Gradually increase the pressure inside the equipment according to design standards and maintain it for a specific duration;
Check the body, welds, and connections for any signs of leakage or seepage.
⇒Precautions:
Ensure the interior of the heat exchanger is clean, and remove air pockets to prevent pressure fluctuations;
Slowly increase and decrease pressure during testing to avoid equipment damage due to sudden pressure changes.
(IV) Corrosion and Fouling Inspection
Corrosion and fouling inspections are crucial for maintaining the long-term operational safety of heat exchangers. The process typically involves the following steps:
⇒1. On-Site Observation
Visually evaluate and record the nature, extent, and progression of corrosion and fouling, relying on sensory experience and professional judgment.
⇒2. Sampling Analysis
Analyze the physical and chemical properties of fouling or corrosion particles to identify issues in the circulation water system and provide scientific support for resolving them.
⇒3. Comprehensive Evaluation
Integrate findings from on-site observation and sampling analysis, along with maintenance records from the previous operating cycle, to evaluate overall performance. Based on the results, propose improvement measures for the next operating cycle.
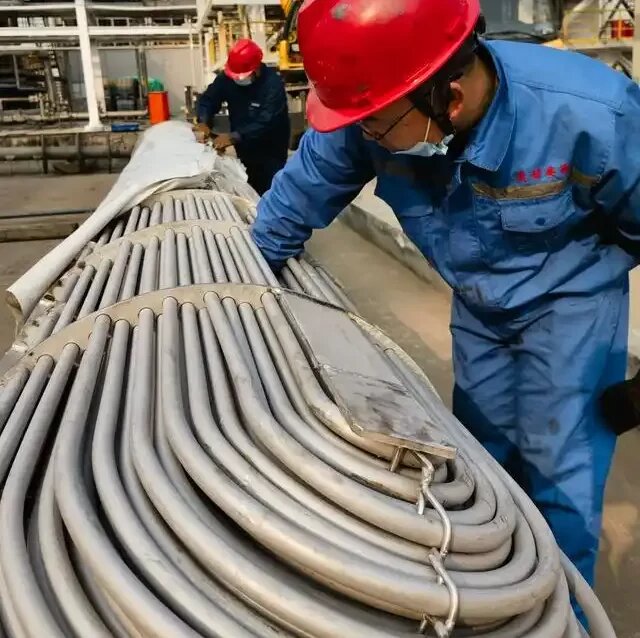