Water cooled wall types, Water wall sizes, Water wall parameters
2024-11-10Leave a message
Types of water-cooled walls
The water-cooled wall is a key cooling component in the boiler system. According to the structural layout and application scenarios, it can be divided into two types: vertical and horizontal.
Vertical water-cooled wall
Front wall type: The water-cooled wall is installed on the front wall of the furnace, suitable for boilers that require high-intensity cooling in the front to ensure temperature control in the main combustion area.
Rear wall type: Arranged on the rear wall of the furnace, suitable for boilers with higher temperatures in the rear to provide sufficient cooling support.
Four-corner type: The water-cooled wall is installed around the furnace to form a closed cooling system. This design is widely used in large boilers, providing a 360° cooling effect and improving the cooling uniformity and thermal efficiency of the furnace.
Horizontal water-cooled wall
Top horizontal type: Located at the top of the furnace, it is mainly used to cool the high-temperature gas in the rising part of the combustion products to prevent overheating in the top area.
Middle horizontal type: Arranged in the middle of the furnace to disperse and homogenize the heat load of the furnace, reduce local overheating, and improve the heat transfer effect.
Lower horizontal type: Located at the bottom of the furnace, it is used to cool the bottom area of the furnace to improve the overall thermal efficiency and stability.
Types of water-cooled walls tube
According to the structural characteristics and heat transfer requirements, water-cooled walls can be divided into different types, each type is suitable for different boiler requirements:
Bare tube water-cooled wall
Structure: Made of smooth steel pipes, without additional fins.
Advantages: Simple structure, low cost, suitable for boilers with low heat transfer efficiency requirements.
Application: Mainly used for small and medium-sized boilers.
Membrane water-cooled wall
Structure: Made of water-cooled wall tubes and diaphragms welded together to form a closed structure.
Advantages: Strong airtightness, reducing boiler heat loss and improving thermal efficiency.
Application: Suitable for medium and large boilers, especially high-pressure boilers.
Fin tube water-cooled wall
Structure: Fins are welded outside the water-cooled wall tubes to increase the surface area and improve the heat transfer effect.
Advantages: Improve thermal efficiency, suitable for boilers with large heat loads.
Application: Widely used in large industrial boilers, especially coal-fired boilers.
Water-cooled wall size and tube size
The size of the water-cooled wall directly affects the overall heat transfer efficiency and structural performance of the boiler, mainly including the following parameters:
Height and width: According to the requirements of different types of boilers, the height and width ratio of the water-cooled wall is generally about 1:3, with a common height range of 1.5 to 20 meters and a width of 0.5 to 5 meters.
Thickness: The thickness of the water-cooled wall is usually around 50mm to ensure sufficient pressure bearing capacity and durability under high temperature and high pressure.
Water-cooled wall dimensions and specifications
Water-cooled wall tube diameter:Common range: φ25mm to φ76mm.
Choice: boiler pressure, flow demand and heat transfer requirements.
Wall thickness:Usually in the range: 3mm to 10mm.
Choice: boiler operating pressure and tube strength.
Tube spacing:Usually in the range: 30mm to 80mm.
Choice: boiler design temperature and tube material, reasonable spacing can ensure heat transfer and structural stability.
Fin height and spacing (for finned tube water-cooled wall)
Fin height: 5mm to 15mm.
Fin spacing: 5mm to 10mm.
Function: Improve heat transfer area and efficiency.
Specifications of water-cooled wall
According to the boiler system area where the water-cooled wall is located, it can be divided into primary side, secondary side and tertiary side, suitable for pipeline structures with different heat transfer requirements.
Primary side:
The main combustion area inside the boiler is the core area of the water-cooled wall, with the highest cooling requirements to ensure that the high temperature of the combustion chamber is effectively controlled.
Secondary side:
The pipeline area from the boiler outlet to the turbine inlet is mainly used for steam transmission and to ensure the balance of temperature and pressure.
Third side:
Located in the turbine exhaust system, waste heat recovery is used to improve the overall heat utilization efficiency.
Performance of water-cooled wall
The performance of water-cooled wall directly affects the efficiency and operation safety of boiler. The following are the key indicators of water-cooled wall performance:
Cooling effect: This is the core indicator to measure the performance of water-cooled wall, which determines whether it can effectively absorb the heat generated by high-temperature combustion, thereby improving the thermal efficiency and operation safety of boiler.
Corrosion resistance: Water-cooled wall is in contact with corrosive gas for a long time under high temperature and high pressure, requiring the material to have high resistance to chemical corrosion and electrochemical corrosion to extend the service life of water-cooled wall.
Pressure bearing capacity: Water-cooled wall needs to maintain structural stability in high temperature and high pressure environment, and have sufficient pressure bearing capacity to prevent deformation and rupture, so as to ensure the safety of boiler system.
Typical design parameters of water-cooled wall
The design of water-cooled wall needs to integrate the operating pressure, temperature and flow rate of boiler to ensure efficient and safe operation. The following are common design parameters:
Operating pressure: The common range is 1.5MPa to 32MPa, and supercritical boiler is higher.
Design temperature: Usually 450℃ to 600℃, and pipes of different materials have different heat resistance.
Flow rate: generally between 1.5m/s and 3m/s, ensuring efficient heat transfer and structural safety.
Material selection of water-cooled wall
Material selection: Water-cooled wall usually uses heat-resistant and corrosion-resistant alloy steel, stainless steel and other materials, depending on the working conditions of the boiler.
SA-210C: This is a commonly used carbon steel pipe for boilers, with good thermal conductivity and certain corrosion resistance, suitable for small and medium-sized boilers1.
12Cr1MoVG: This is a low-alloy steel pipe with high heat resistance and corrosion resistance, suitable for high temperature and high pressure environments1.
SA-213T91: This is a heat-resistant alloy steel pipe with excellent high temperature resistance and corrosion resistance, suitable for large high temperature and high pressure boilers1.
SA-106C: This is a medium carbon steel pipe suitable for general industrial use, but not as high temperature and corrosion resistant as the above materials
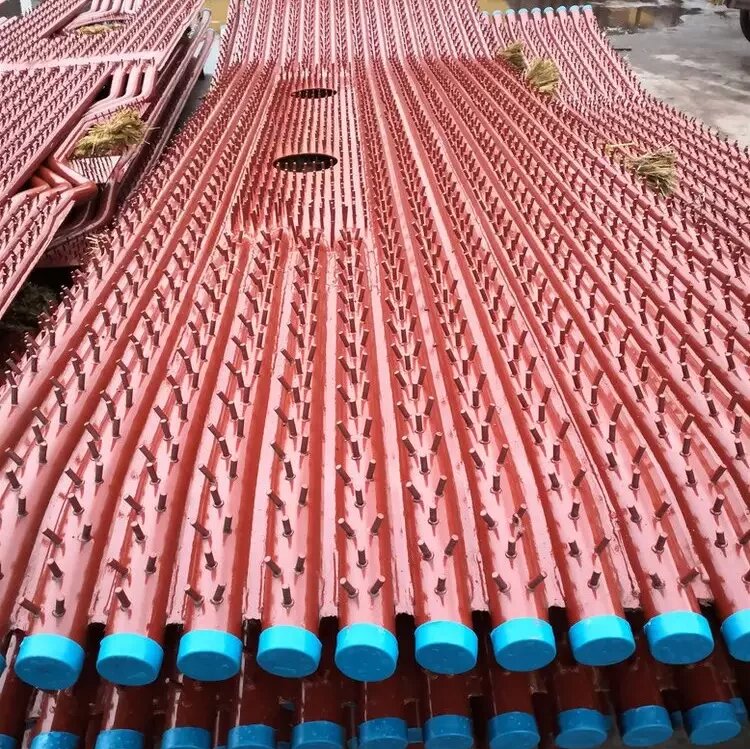